Reliability and Maintenance Management Training
- build your maintenance team
- increase plant reliability
- optimize maintenance costs
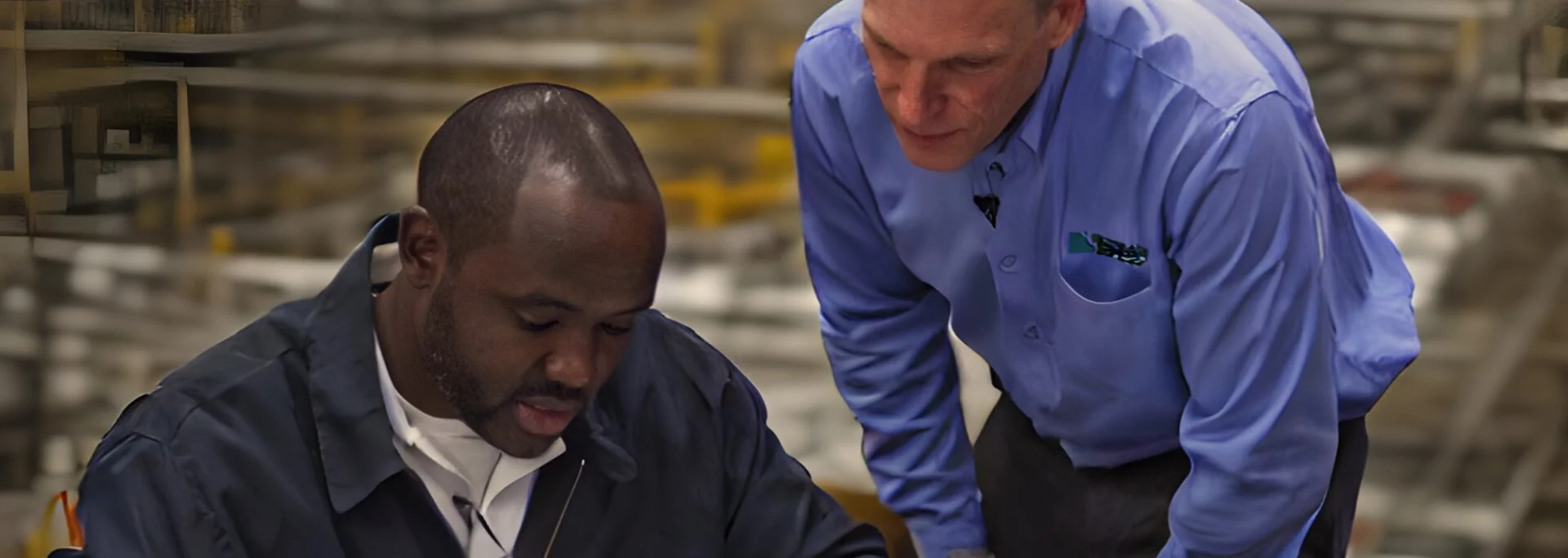
What’s holding your reliability and maintenance improvements back?
- Reactive maintenance
- Lack of consistency
- Unplanned downtime
- Lack of knowledge
- Everyone works on their own priorities
- High maintenance cost
- Unskilled personnel demanding attention
Build your team’s cohesion and focus
It creates unity. It grows confidence. It allows the team to refocus and do their job with energy and excellence.
With IDCON’s reliability maintenance management training, you’ll know your team is equipped to do their best work…today.
Reliability and Maintenance Training Options To Fit Your Needs
Training and Coaching Topics
- Managing Maintenance
- Operations and Maintenance Partnership
- Operator Based Care (Autonomous Maintenance)
- Planning and Scheduling
- Preventive Maintenance
- Reliability Engineering
- Reliability -Based Spare Parts Management
- Root Cause Problem Elimination
- Shutdown Turnaround Optimization
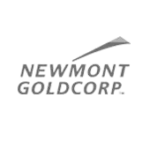
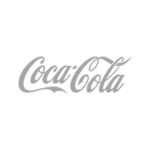
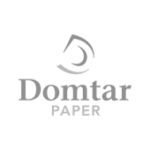
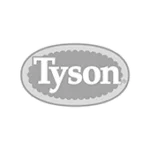
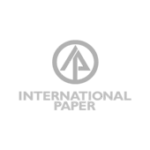
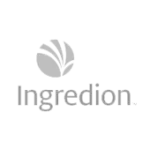
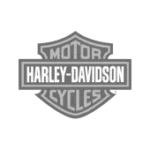
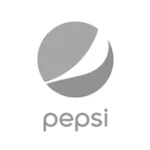
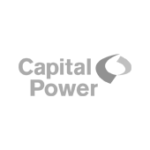
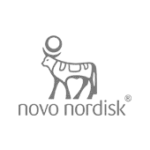
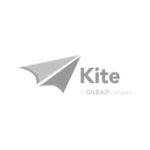
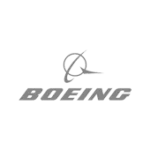
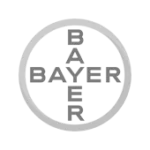
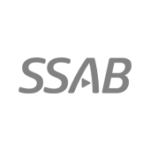
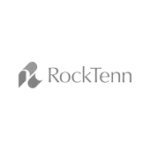
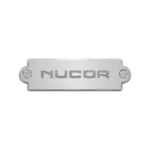
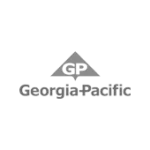
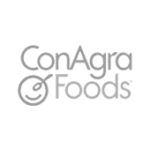
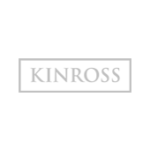
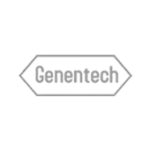
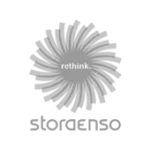
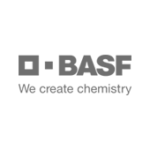
Are You Ready to Improve?
"*" indicates required fields
Reliability and Maintenance Learning Options
Learn On Your Own
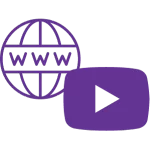
Articles and Videos
Our website and YouTube channel have hundreds of articles and videos for quick lessons in maintenance and reliability topics.
View Free Resources
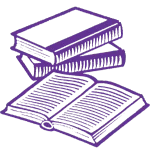
IDCON Books
Our eleven Reliability & Maintenance books offer practical knowledge. Written by our experts, who’ve spent decades in the reliability and maintenance field.
Buy the Books
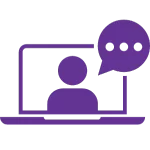
Online Training
Through videos, downloadable content, and knowledge tests you’ll go at your own pace learning the fundamentals of reliability and maintenance concepts.
View the Training Topics
Instructor Led Training and Coaching
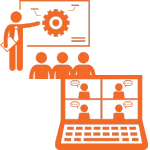
Public Training Courses
Five of our most popular training courses are delivered through our public training events. Your team can join us in Raleigh, NC or online via Zoom.
View the Event Schedule and Register.
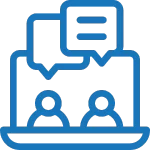
Online Learning with Coaching
Combines On-Your-Own learning with feedback and coaching sessions. This unique training includes practical on-the-job exercises, videos, downloadable tools, and 1.5 hours of remote coaching with an IDCON Consultant.
Learn more
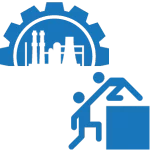
Onsite Coaching, Training, & Consulting
Take your reliability and maintenance knowledge to the next level. Our coaching, training, and consulting ensures your team has the knowledge and skill to sustain performance and plant reliability.
Contact Us
What our students say...
Reliability and Maintenance
Training and Coaching Topics
We can customize our trainings to fit your needs.
Work Management / Planning and Scheduling
If you want to improve efficiency, effectiveness and reduce overall maintenance cost over time, you must train your entire organization in work management.
Materials & Spare Parts Management
Having the right spare parts, in the right place at the right time is critical. This training provides real solutions for your materials, spare parts, and storeroom management problems.
Develop & Manage Preventive Maintenance
A preventive maintenance program enables your plant to identify and minimize equipment failures. Learn to set your own cost effective process and PM techniques.
Root Cause Problem Elimination
Our Root Cause Problem Elimination training focuses on eliminating problems, not just analyzing them. You’ll learn to effectively tie cause and effect together to prevent the causes from happening.
Results Oriented Reliability & Maintenance Management
Accelerate your improvement initiatives and increase awareness for Reliability and Maintenance across the organization. If you need to understand the gap between where you are and where you need to go, this course is for you.
Shutdown / Turnaround Management
Many industries spend the majority of their maintenance budget on shutdowns. But what if things were different? We’ll teach you how to stay on budget and minimize downtime through a 6-step process that focuses on countdown actions, tools, and resource optimization.
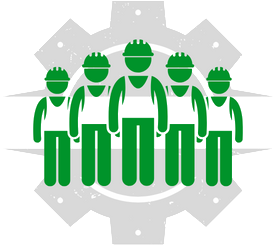
If your maintenance team is lacking skills or falling behind, it's time to take action.
We would love to talk and see how we can help.