Reliability is a term is commonly used in the manufacturing industry.
Many organizations are using reliability to describe their predictive maintenance department.
To me reliability has always encompassed the measurement of manufacturing efficiency and includes Operations, Maintenance, Engineering and Spare Part Stores as the major players.
Together these departments shall deliver Manufacturing Reliability and we know that better reliability results in:
- Improved safety.
- Faster manufacturing throughput.
- Lower manufacturing cost.
- Lower energy consumption.
There are many ways to measure reliability in manufacturing.
The least complicated is to divide Quality Tons Manufactured by Capacity Quality Tons.
However it is beneficial to break up this equation in three elements:
% Quality Tons x % Time Efficiency x % Speed performance.
If each of these is 95% the total manufacturing reliability is 85.7%.
By measuring these three elements it will be easier to pinpoint where the biggest losses are.
It is not uncommon for organizations such as paper companies to only measure the time element of this formula often expressed as % availability or “% time we have sheet on reel” for a paper machine.
To me this is wrong because you might have a high availability but you might have to scrap all products made or you are not running at full speed.
I see the equipment reliability component of manufacturing reliability as the revenue side of what the maintenance organization does and the process reliability component as the results of what the operations organization does.
The maintenance organization is supported by efficient and cost effective stores and engineering is responsible for cost effective design including maintainability and reliability considerations.
The roles of these departments must be clearly defined and their joint goal should be manufacturing reliability. They are in a relationship of equal partners and never in an internal customer relationship between each other. (See article in October 2011 PPI issue).
Organizational Silos
One of the biggest obstacles to overcome is that organizations are set up in silos with different goals. Watch my YouTube Video “Are you on an Reliability Happy Island?”
For the engineering organization it is not necessarily so that lowest Life Cycle Cost (LCC) over more than fifteen years of ownership is most important.
Costs as a result of poor maintainability and reliability design might consequently be much higher than necessary over the years equipment is owned and operated. In most organizations the project manager is driven and awarded if projects come in on time and under budget not by lower LCC.
Key operations and maintenance people are often not included in the early specification phase of a project and many good ideas are lost. It is not uncommon that basic documentation such as detailed bills of materials is left out.
This will lead to difficulty to optimize stores and much extra work to document these bills of materials later.
The operations organization is rewarded by tons manufactured. The maintenance organization is measured primarily by cost as set in the maintenance budget and stores are often challenged to reduce inventory value.
It is not necessarily so that these measurements are wrong but if applied in organizational silos they lead to sub optimization and total results will suffer.
To improve this situation mills need to rethink their departments roles and goals and bring them together in a partnership work system with one goal expressed as manufacturing competitiveness e.g. Quality Tons/Cost (instead of Cost/Ton) to articulate the focus on manufacturing reliability.
All other goals and performance indicators shall drive actions to support this goal.
Increased reliability in manufacturing will drive down costs
Cost to achieve improved reliability is important.
Most of the cost consists of implementation of better maintenance and operations practices and training of your employees to do better with what they already have.
After a short period of increased costs reliability will improve and manufacturing costs including maintenance costs will continuously go down over many years. An established fact is that improved reliability is a major driver to improve safety and costs.
To simplify, there are three ways to reduce maintenance costs:
- Cut the cost.
- Prevent Maintenance.
- Execute remaining maintenance more efficiently.
Cut the cost
To just cut the cost instead of improving what drives cost is the wrong thing to do.
If maintenance costs are cut by layoffs of people and no improvements in systems, processes and practices are done it will within one to two years lead to more overtime, more use of contractors more total maintenance hours, lower reliability and higher costs.
Some valid maintenance work can be deferred with the risk associated with that but sooner or later the work must be done.
To just cut the cost is a short term action with expensive long term results. My observations are that this is not as common as it used to be but it is still far from uncommon.
Over the years this will repeatedly happen in mills where a well defined, documented, communicated and executed reliability and maintenance strategy is absent. 60% of mills have had more than three mill managers, production managers and maintenance managers in the last ten years per response to a survey on www.idcon.com .
If you do not have a reliability and maintenance strategy to execute there is a risk that each new manager will implement a new program. This will very often confuse the organization and ongoing improvements will discontinue.
Prevent Maintenance
To prevent maintenance work from occurring is the right thing to do.
Whatever name you give your maintenance program it will always be important to execute the fundamental elements of maintenance better and better. To prevent maintenance or maintenance prevention includes the following must do essential elements.
- Right equipment. Procurement of new equipment should be based on lowest Life Cycle Cost and include reliability and maintainability design.
- Lubrication. It is still one of the most important things to do well by trained people.
- Alignment must be done to a precision level with considerations to operating temperature, pipe strain, number of shims etc.
- Filtration of hydraulic fluids, lubrication oils, seal water for mechanical seals must be done to specified levels.
- Balancing must be done to precision level.
- Operating Practices are essential to prevent maintenance. Operators must understand how to operate equipment and the impact wrong operating practices have. E.g. how to start a pump, what happens to an electric motor if it is dirty or is frequently started. Redundant equipment should be shifted to operate same amount of hours etc.
- Fixed Time Maintenance is very seldom justified and often leads to over maintaining. Only if it is justified based on failure developing times and distribution of failures in time it can be cost effective to do.
Execute remaining maintenance more efficiently.
Maintenance Prevention will increase reliability and reduce maintenance work. All work cannot be prevented so remaining work should be done more efficiently by skilled people in the following process:
- Identify work early through good inspections of equipment and disciplined priorities.
- Plan work.
- Schedule work.
- Execute work according to schedule.
- Record work done.
- Use recorded information to trigger a Root Cause Problem Elimination action.
What is the secret?
The secret is that there is no secret.
The above concepts are very well known and documented in hundred of books the last fifty years. So why is it so difficult to do something so simple well?
One of the reasons for this is that companies often make it much more complicated than it is. New names on well known concepts confuse people.
They think it is another new program that will only last until we get the next manager so why make too much effort to buy in?
We need to realize that to improve maintenance is 90% about people and 10% about technology and as engineers we often like to deal with technology more than with motivating people.
Most maintenance people like gadgets while they might not like to change to working in a disciplined system. A reactive system rewards action and extra income through overtime.
The big challenge is to change the way maintenance work is viewed by top management.
Maintenance is often controlled way too much based on cost instead of the results delivered through efficient maintenance work.
As mentioned above, the results of maintenance work include equipment reliability followed by better safety and lower costs. Maintenance managers are often not aggressive enough.
As a maintenance manager you need to know how good your organization is compared to how good it can become. Then you need – a well documented plan showing how you are going to close that gap, what benefits you will deliver and how much it will cost. Then you need to sell that plan to top management and then to the people in your organization that will help you deliver the plan over the next three to five years.
Remember that almost all improvement initiatives have to be executed by your front line organization; if they are not supported to execute nothing will be delivered.
As the picture describes the front line organization in a bigger mill includes planners, supervisors, coordinators, operators and maintenance crafts people.
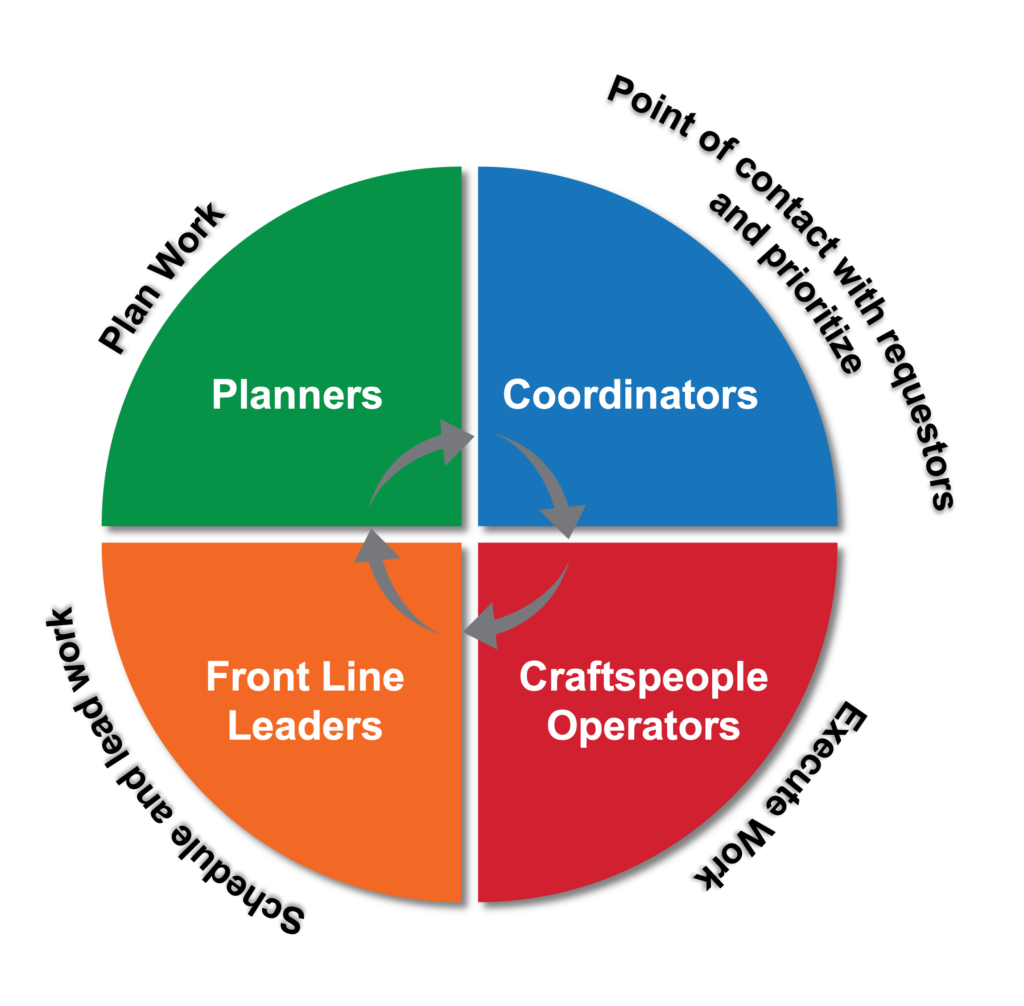
(Manufacturing Reliability)
Christer Idhammar is a world renowned and award winning Reliability and Maintenance Consultant and Guru. He is the Founder and CEO of IDCON, INC in Raleigh NC, USA; A reliability and maintenance training and consulting company to the Pulp and Paper Industry worldwide since 1972.