We all know that in a reactive maintenance organization 60 – 70 % of crafts people’s time is wasted on finding out what to do, finding parts and materials, etc.
We also know that the solution to this situation is to become more proactive and in control. This can be done by better condition monitoring, planning of work and scheduling of work combined with an efficient store including an accurate bill of materials.
Best organizations I have worked with have very little wasted time because of good leadership and an efficient work management process.
More importantly they have higher reliability and faster production throughput and consequently lower manufacturing costs. They see lower costs as an outcome of higher reliability and faster production throughput.
Less efficient organizations are more shortsighted and put an emphasis to stay within the maintenance budget rather than doing what is necessary to deliver stable and reliable quality production output.
Maintenance managers are often driven to stay within budget to the extent that reliability suffers. As a maintenance manager you need to have a three to five years plan covering:
- How good your organization is today.
- How good it can become.
- How you are going to close this gap.
- How much it will cost.
- How much savings in reliability and costs will be generated.
All the above must be supported with a strong business case so you can sell it to decision makers.
Remember, most of this is common sense so do not over complicate it and the good thing is that it is not a question of much capital money, if any, it is a matter of doing better with what you already have.
As part of your business case you should know where your maintenance organization spends its maintenance hours. This absolutely does not mean that you do any time studies. Instead you divide where time is used in three categories:
- Corrective maintenance
- Preventive maintenance
- Continuous improvement
Corrective maintenance is all maintenance done to correct a failure or a break down. It can be done in four different ways:
- Planned and Scheduled
- Only Planned.
- Only Scheduled
- Break in work in schedules
Number 1 and 2 is where you like to spend most time.
The fact is that most organizations spend the majority of their time for weekly and daily maintenance in number 3 and 4. During shut downs the situation is better but if you spend more that 5% of your time on number 3 and 4 during a shut down you need to improve on this.
Preventive maintenance (PM) is all maintenance done to prevent failures or to discover failures before they develop to a break down. If your PM has the right content and is executed right your organization shall not be in a reactive mode.
Continuous improvement is work doneto do Root Cause Problem Elimination (RCPE). In a reactive organization this is close to zero maintenance hours even if organization has a process and people have been trained.
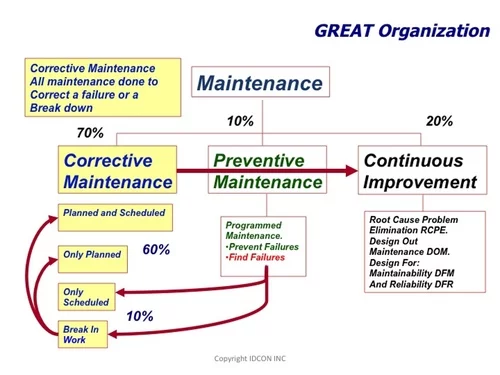
In this actual example of a World Class or Great Organization time is used as in the example in Figure 1. All preventive maintenance including basic inspections, predictive maintenance and lubrication is about 10 % of all maintenance hours if all tasks are optimized. Only scheduled and break in work is 10% Planned and scheduled work is 60% and hours for Continuous improvement are 20%.
Reliability is steadily increasing and costs are decreasing.