What is Industrial Maintenance?
Industrial maintenance is a comprehensive process crucial to the reliable operation of various industrial plants, mines, and mills. It extends beyond simple repairs, involving a systematic approach to condition monitoring, fixed time maintenance, and corrective maintenance approaches for industrial equipment.
The primary goal is to ensure that the assets operate safely, efficiently, and with minimal unscheduled downtime. It’s not just about repairing broken; it’s about proactive strategies to prevent breakdowns and to identify potential breakdowns early, thus maximizing operational efficiency and productivity. By extending the lifespan and reliability of physical assets, industrial maintenance plays a key role in long-term financial results for an industrial operation.
Industrial Maintenance's Scope
One aspect of the management of industrial maintenance is its wide-ranging scope. It covers everything from routine tasks like lubrication and calibration to complex overhauls and replacements. This process is integral to maintaining the heartbeat of an industry’s operations, ensuring that machines and systems are in optimal condition and that any potential issues are addressed before they escalate into major unscheduled downtime. The field constantly evolves with technological advancements, requiring professionals to stay abreast of the latest techniques and tools for efficient maintenance management.
Industrial Maintenance Strategies
As mentioned before, industrial maintenance includes routine tasks as well as more complex activities. The overarching aim is to minimize unscheduled downtime by either preventing failures before they occur or finding them early to enable a scheduled stop to do planned repairs, thus ensuring continuous and efficient production. Maintenance organizations employ a variety of strategies to achieve this:
This proactive strategy involves maintenance tasks that directly prevent failures or extend life of components. Examples of tasks that extends life are lubrication, precision alignment of shafts, balancing of rotating equipment, and operating practices. The goal is to perform essential care of the equipment continuously before any signs of wear or failures are eviden
Corrective Maintenance
The key to an efficient corrective maintenance strategy is to make sure that most corrective maintenance jobs are planned and scheduled. By establishing a predictive maintenance (Condition Monitoring) process, it is possible to predict a large portion of failures before there is a breakdown and allowing time to plan and schedule the corrective job. This strategy is crucial for safely and efficiently restoring machinery to its operational state.
Predictive Maintenance
Another critical maintenance strategy is predictive maintenance, which relies on subjective and data-driven insights to predict when equipment might fail. By monitoring equipment conditions through various diagnostic tools, human senses, and sensors, maintenance teams can anticipate problems before they occur, enabling planning and scheduling of the corrective work.
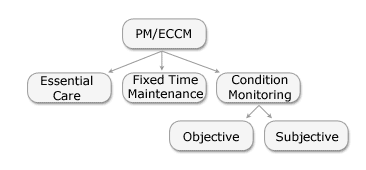
Industrial maintenance is not just about the technical aspects of machinery care; it involves a strategic approach to managing physical assets. This includes understanding the lifecycle of each piece of equipment, analyzing cost-benefit ratios of various maintenance strategies, and implementing best practices in asset management. The goal is to strike a balance between minimizing operational costs and maximizing equipment performance and longevity.
Improving Industrial Maintenance Management
Before delving into specific improvement strategies, it’s important to recognize that industrial maintenance management is a field that demands both technical proficiency and strategic foresight. Improving in this area means not only acquiring the right technical skills but also developing a mindset geared towards continuous improvement and preventive thinking.
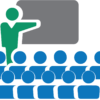
Education and Certification: Gaining formal education and certification such as CMRP, CMRT or others. IDCON’s Reliability and Maintenance courses offer the best education that prepares you for certifications.

Hands-on Experience: Through internships or apprenticeships.
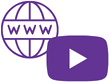
Keeping Up with Industry Trends: Staying informed about new technologies and practices.
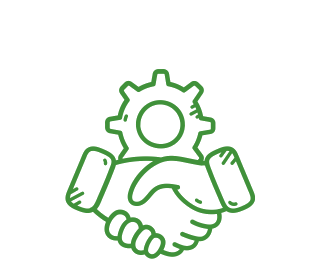
Networking and Professional Development: Attending industry events and workshops. Meet IDCON at these conferences: Marcon, SMRP and Reliable Plant.
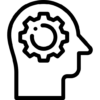
Developing Key Skills: Such as problem-solving, analytical, leadership, and communication skills. IDCON helps by coaching your team onsite.
How IDCON Helps Improve Industrial Maintenance Management
At IDCON we are committed to helping organizations optimize their maintenance management practices and processes. Our approach goes beyond merely implementing best practices; it involves cultivating a culture of maintenance excellence across all organizational levels. By focusing on strategic improvements, leveraging advanced methodologies, and empowers companies to optimize their maintenance operations.
Cross-Functional Collaboration: We promote a culture of cross-functional collaboration. This involves encouraging strong communication and cooperation between maintenance teams, operations staff, engineering departments, and management. Such collaboration ensures a comprehensive approach to maintenance, where knowledge and responsibilities are shared for more efficient and effective maintenance process.
Training Personnel: Knowing the value of a skilled maintenance team, we focus on training personnel in both management, technical and problem-solving skills. Our training ensures that the whole maintenance organization is fully equipped to handle complex tasks, adapt to new technologies, and effectively troubleshoot issues.
Robust Analysis: By analyzing comprehensive asset performance data, we assist you in making informed decisions. This includes scrutinizing maintenance records, operational data, and failure patterns to optimize maintenance schedules and improve overall equipment effectiveness (OEE).
Develop Maintenance Equipment Strategies. We believe that Preventive Maintenance/Essential Care and Condition Monitoring documentation is critical. Our method is based on symptom modes rather than failure modes. We also find the right balance for RCM or FMEA for your needs. Our approach is risk-based, emphasizing cost effectiveness PMs, and reduced risk of safety incidents and equipment failures
Structured Work Management Processes: We understand the importance of effective communication and resource allocation in industrial maintenance. Our structured work management processes, including work orders, ensure clear communication of maintenance tasks, proper prioritization, and safe and efficient execution. Reduce response times and increase the productivity of maintenance teams.
Technical Resources: When you have poor technical information, Bills of Materials, or Preventive Maintenance routes and don’t have resources to fix the problem, let our Technical Consultants do the work.
By integrating these strategies, we help organizations not only improve their industrial maintenance practices but also achieve higher reliability, productivity, and cost efficiency in their operations.
For organizations seeking to optimize their industrial maintenance, partnering with IDCON offers a path to improved reliability, reduced downtime, and cost savings. Contact IDCON today to embark on a journey towards maintenance excellence.