Manufacturing facilities know downtime is money. Every hour you are offline for a shutdown (SD) is costly from both lost revenue and cost of the workforce employed to maintain the facility. That’s why you must optimize shutdown programs.
This article will discuss the 5 steps to best practices so you can optimize shutdown programs in your manufacturing plant.
Step 1: Strategic Review
Step 2: Work Scope Review
Step 3: Execution Planning Review
Step 4: Integrated Schedule Review
Step 5: Close Out Review
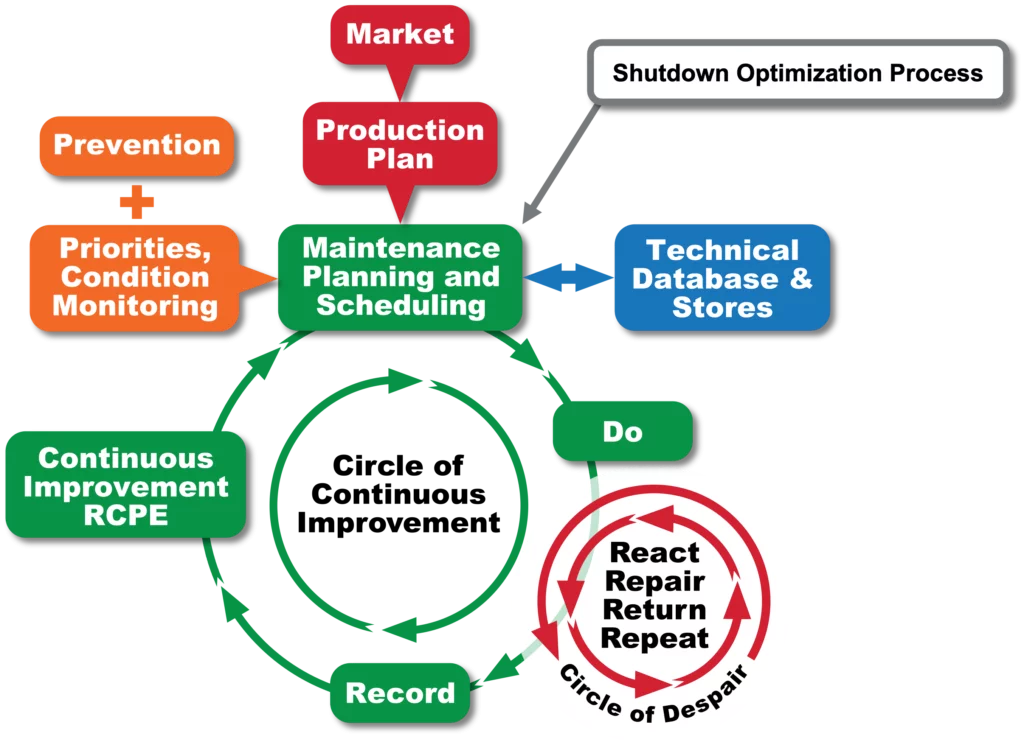
Step 1: Strategic Review
By optimizing your SD timing and drivers, you’ll generate a significant opportunity to improve mechanical availability, particularly if your facility has alternate production capacity and intermediate storage.
The best practice is to complete a strategic review; by doing so you’ll be able to optimize the timing of any shutdown taking interactions with other plant and facility operating areas into account.
Step 2: Work Scope Review
Reducing the cost of SD is easy when you eliminate work scope, however, it’s not as easy to account for the consequences of the change.
In a best practice program, plant personnel are assisted through a risk-based decision-making process…achieving cost savings by eliminating work, deferring work, or changing techniques to deliver the same or better results with lower risk exposure.
Step 3: Execution Planning Review
The third step in your SD process should be the execution planning review; this is designed to prepare the best contracting and work plan to reduce the mechanical path duration.
The best practice is to go through all possible options ensuring it meets the SD requirements. Once the contracts are in place, you then need to review the overall critical path for the turnaround. You should review in detail work patterns, parallel activities, rescheduling techniques, and labor-loading profiles; make any revisions and finalize.
Step 4: Integrated Schedule Review
This step looks at the process critical path in order to reduce overall raw material into product out time and minimize the risk of schedule deviations.
The best practice is to apply proven techniques to shutdown, de-commissioning, re-commissioning, start-up schedules, and procedures. You must have a best practice team in place whose job it is to focus on integrating the process and mechanical schedules to further minimize unit downtime.
Step 5: Close Out Review
This is an integral step in the process…you must ensure that lessons learned during the shutdown are documented and used to enhance future shutdown plans.
If you bypass this step you are bound to make the same or similar missteps at the next shutdown.
By following these steps you will be adding efficiency and minimizing downtime.