Reactive maintenance is here defined as all maintenance work that was scheduled less than 20 hours before it was executed.
It makes sense that there is a strong correlation between safety incidents, injuries and reactive maintenance. In a reactive situation you might not take the time you should to plan and think before you take action. The urgency also call out the so common hero in maintenance crafts people and they take risks they should not take.
During Pima’s conference in New York June 2003 a speaker referred to a study done by one of the major Pulp and Paper companies; they had concluded that it was 28% more likely to have an incident when maintenance work was reactive versus planned and scheduled before execution.
Because of the strong correlation between reactive maintenance and safety incidents and injuries I suggest that organizations use this as a key performance indicator.
To measure it will drive down both safety incidents and the volume of reactive maintenance. This in turn will result in increased quality production throughput and consequently lower maintenance costs.
Since December 2003 we have done a survey on the relationship between reactive maintenance and safety incidents. In mid January we can show the following empirical data. Please go to www.idcon.com to participate in this survey. Click on “Monthly Survey” to answer three simple questions.
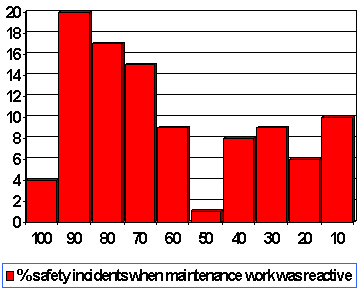
Reference IDCON Safety/Reactive maintenance Survey as of 2004-01-15
In mid January the results shows that 66% of all respondents estimated that more than 60% of all safety incidents occurred when a maintenance job was executed as reactive. This data include respondents from many industries. Pulp and Paper Industry represented 36% of all respondents.
It is a well known phenomenon that many maintenance improvement initiatives are too short lived to generate the substantial results that are possible.
One of the major reasons for this is the mobility of top management and the new initiatives that then follow. This disrupts and confuses organizations and after many repetitions of the above people loses faith in the longevity of the initiative and will only pretend to implement improvements.
According to the Pulp and Paper Safety Association www.ppsa.org the Total Case Incident Rate per 100 employees and year (TCIR) have gone down from 8.92 in 1990 to 3.05 in 2002, and if we go back twenty years the results are more impressive.
Why have the industry produced these results? It is not through better planning and scheduling of maintenance, because that is still not being done much better than 1990.
I think the answer is that safety has had a long term focus without constant changes even when top management changes. Another important reason is that it is being measured and there is a positive or negative consequence depending on the results.
My message is that to go the next step in reducing TCIR an important tool is much improved planning and scheduling of maintenance. It is too important to ignore and it does not cost much money to improve.
To help me do a better job at addressing the right things in this column I welcome input from the readers, please send ideas to [email protected] attention Christer Idhammar.