Is your Preventive Maintenance Program on a summer break or does your team perform the critical essential care tasks year-round?
An effective Preventive Maintenance program must be executed consistently regardless of the season!
This is an example from a process plant that we have worked with the last few years. In a meeting with the Leadership team of the plant, they agreed with us when we talked about Preventive Maintenance (PM). The Plant Manager responded, “We want to do all these things, but we don’t. Can you tell us why we don’t?”
Definition:
Preventive Maintenance = All maintenance done to prevent a failure (life extension) and detect a failure early (Condition Monitoring) before it impacts the process.
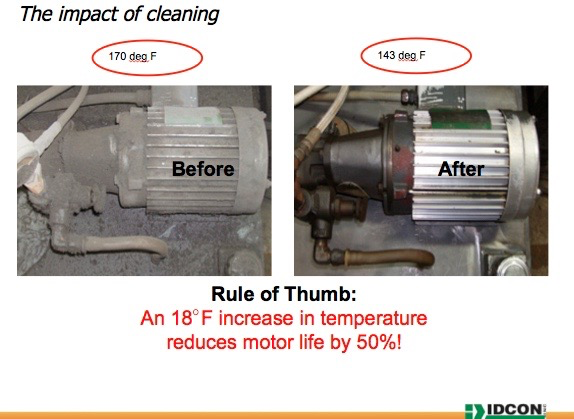
The client was looking at all the newest technologies out there like IoT (internet of things), cloud based data, and connecting smart devices with your mobile apps.
These are all good things at the right time, but you have to have the basic processes and simple tools in place first.
Basic processes include Essential Care such as, cleaning, lubrication, alignment, balancing, mounting procedures, operating procedures etc.
For example, if you notice the temperature rising on a very dirty AC motor, start with cleaning and basic PM inspections.
You can use simple tools like an IR-gun and a vibration pen to check the condition, and a stroboscope to inspect the coupling on-the-run. Train the people doing inspections to understand the principals of how the motor and coupling works, and the basic failure modes for key components like the bearings and the windings.
Also, train them in how to use the inspection tools. If you document and describe these inspection instructions on a PM route or a work order you will get consistent execution of your PM task.
Don’t have time or resources to train them in the basics? Send them to our Essential Care and Inspections Techniques seminar
Back to that client- when we looked at the inspection routes and PM work orders in place we saw they put some good thoughts into documenting Essential Care and Condition Monitoring for some of the equipment. Still, there were many inspections that only said, “Inspect motor.”
One of the maintenance technicians showed us the PM work order and his written comments said, “The motor is still there!” Humor is great in this case, but details are needed on what to inspect, how and where to measure, and the acceptable range.
The maintenance department focused a lot on doing vibration analysis and electrical dynamic and static testing of larger AC motors.
We found that many motors failed due to under or over-lubrication. Do we need to focus on detecting the bearing going bad before we attempt to make sure that we have optimal lubrication of the bearings?
The lubrication issue was identified through the Root Cause Problem Elimination process of several AC motors that failed.
Do PM’s on the AC motors as long as it is cost-effective, i.e. Condition Based Maintenance costs less than Operate To Breakdown.
Based on our PM evaluation we found the client should do both, the right lubricants, at the right time, the right amount, and have vibration analysis to provide both Essential Care and Condition Monitoring.
As time passed, with our assistance, the client developed PM inspections with the right frequency, trained the inspectors, and executed them on time. The PM inspections generated quality work requests that were turned into work orders for Corrective Maintenance and were planned and executed according to the schedule.
And they were making progress until…summer!
During and after summer vacation we noticed the PM compliance went from over 90% to less than 20% and this went on for several months after the vacation season. An effective PM program requires good processes, documentation, tools, and execution of tasks.
The discipline to continue the program had not been anchored. We believe that the leadership team in Operations and Maintenance needed to get more involved to make sure that processes are executed and compliance is reported.
Preventive Maintenance needs to be executed according to the schedule despite vacation season, deer hunting season, or moose hunting season.
What season will decrease the efficiency of your PM program?
Contact IDCON to learn how to jump-start or tune up your Preventive Maintenance Program with a PM focused assessment.