It is easy to make mistakes when performing a Root Cause Failure Analysis (RCFA) – we have all done it.
Common RCFA mistakes includes overwriting the problem statement. An essay is not the way.
We tend to want to write everything that happened and everything we know. This makes it very confusing for the people who are tasked with solving the problem.
Here is an example of observations from a cavitating pump situation:
- Pump sounds as if it is cavitating
- The bearings are hotter (183F) than normal
- The valve upstream is open 75%
- The operator said she heard a noise around the pump at 4:30 am this morning
- The packing is leaking too much water
- The pump is not delivering enough flow (based on flow meter)
- There is a leak in the inlet pipe 4 ft before pump inlet
Much of this information is useful, but some is irrelevant. I have seen many cases where all of this information is used as the problem statement, and we want to avoid that.
In the list above, we have seven different problems with different objectives. So how do we deal with this? One of the skills in Root Cause is to be able to take a situation and transform it into a problem statement.
In this situation, I’m going to choose pump flow as the problem statement because the most important problem to solve is why we don’t have pump flow. The cause-and-effect diagram IDCON uses – the “How Can Diagram” – for this problem is shown below:
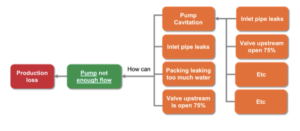
The trigger is production loss, and the problem statement is “Pump not enough flow.” The statement has one object – pump and not enough flow. On the other end of the chart, we have potential causes. Notice that information from our list earlier is in the diagram.
Pump cavitation could definitely cause the pump to have no flow. An inlet pipe leak could be a cause by itself without having the cavitation.
Packing leaking too much water is not that likely. It is easy to check if the valve upstream being open is the problem. It depends on where that valve is located, but if could definitely be the culprit. The valve that’s upstream open only 75% can cause the cavitation, and it could be a number of other things, but we don’t have any other information.
In summary, convert that situation into a problem statement and solve the problem you want to solve one at a time. If you’re trying to solve too many problems at the same time, it gets really tricky to do Root Cause.
Learn about the other common RCFA mistakes that a lot of people make in my video series on the topic. Do you want to stop making these common RCFA mistakes? Take our course in Root Cause Problem Elimination