Root cause confusion
There is a lot of confusion between diagram, tools, software and company names for root cause. This video series, featuring Torbjorn Idhammar, is going to help you understand that it’s not the about tools you decide to use but rather how you engage your team in thinking about problems at your plant, mine or mill.
When clients ask us for a reliability and maintenance assessment, one aspect we review is their process for eliminating problems. We ask an open ended question “How do you eliminate problems in the plant/mill/mine?” and we’ll get answers like “We use Apollo”, “We use 5 why”, “we use Prologic”, “we use histograms”…you get the picture. They are talking about the tools they use not the process they follow.
The tool you use doesn’t matter, it’s the process
There’s nothing wrong with using a tool to help you document, but sometimes we think because we use this amazing tool, it’s the process but it really isn’t.
The #1 most important part of the root cause process
The heart of solving problems is the thinking process. Then you need to have a problem solving method. IDCON developed a method called Root Cause Problem Elimination it’s follows the basic steps of Root Cause Failure Analysis with a key difference…you aren’t just documenting the problem you are implementing the solution. And you are getting much deeper into why problems happen. Here’s a great article about the 3 main causes that create problems at plants. Very simply put they are:
- Technical
- Human
- Process
What we find is that one may lead to the other. Here’s an example of how these three are connected. The example is that production was stopped due to a failed component.
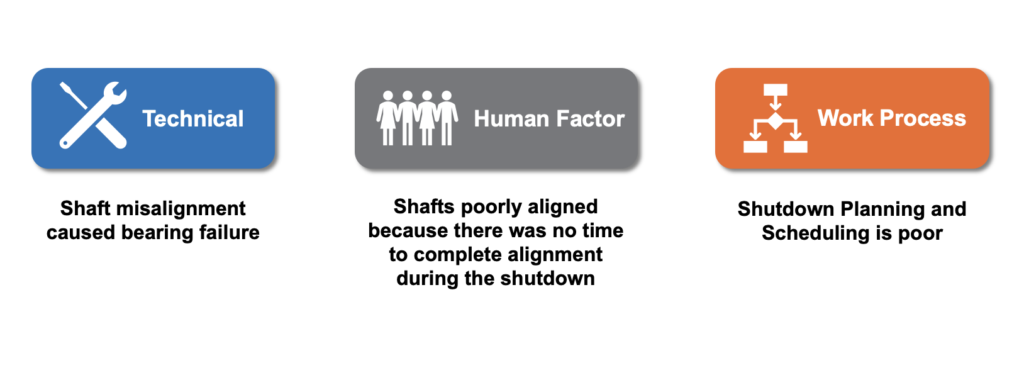
The next step in your problem solving process
Then you need to decide on the documentation method or tool. I will caution against using Fishbone…if you want to know why here’s an article where I discuss my thoughts about Fishbone diagrams
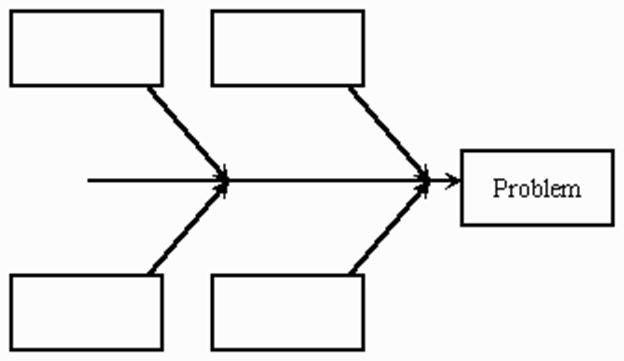
The 8 steps of the root cause problem elimination process
When you are developing your process for solving your most pressing problems be it equipment, process or production there are 8 steps that you should follow. When we provide training or consulting to clients in the RCPE process we go into detail of each of these steps. Get trained in Root Cause Problem Elimination.
- Determine your triggers
- Collect the data- physical evidence; What, where, when, changes in time, similar object
- Write a problem statement
- Determine the possible causes. Use tools like a How-Can diagram, etc Then collect more data on the possible causes to eliminate causes
- Select most likely cause
- Determine solutions to the most likely cause
- Select solution
- Eliminate the problem
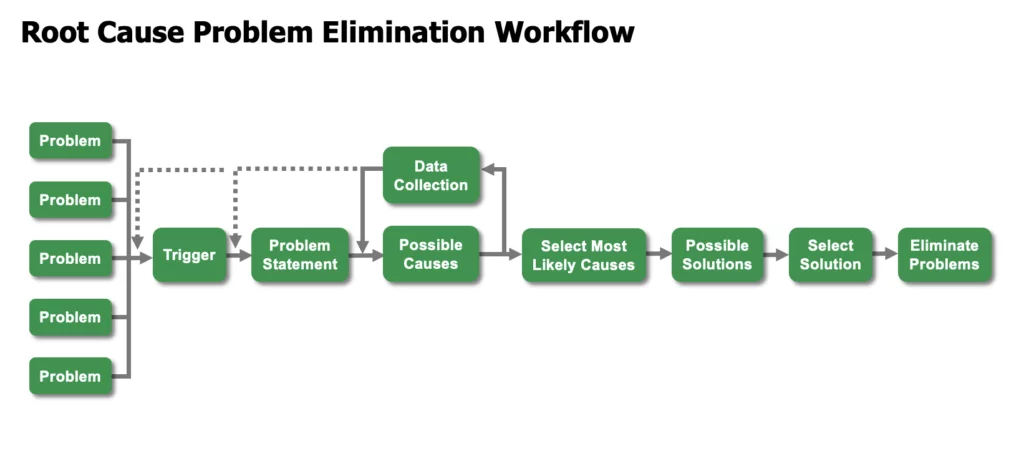
Watch part 2 of this series where I go deeper into how to use creative and critical thinking to solve problems and eliminate them.
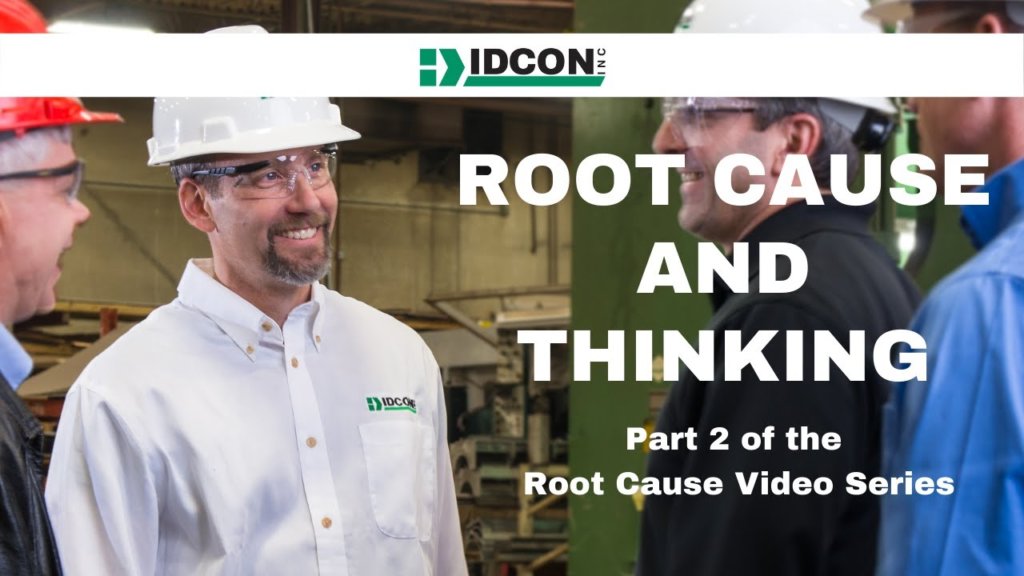