I recently visited a plant in South America for an assessment.
They had done some really good things in the plant over the past 2-3 years, but they had not been able to achieve stable reliability performance of their production lines. They were hovering around the high 70s [%] for their Overall Equipment Efficiency (OEE).
The business consultant they had been working with had coached them on focusing on “low hanging fruit” and “quick results” in order to get quick financial impacts.
This sounds great! We all want the quick fixes with high impact, right? The mill could also show some great pockets of success.
There is nothing wrong with focusing on getting quick results in maintenance, but there is a major problem with ONLY focusing on quick results and not long term reliability.
Let me explain what I mean.
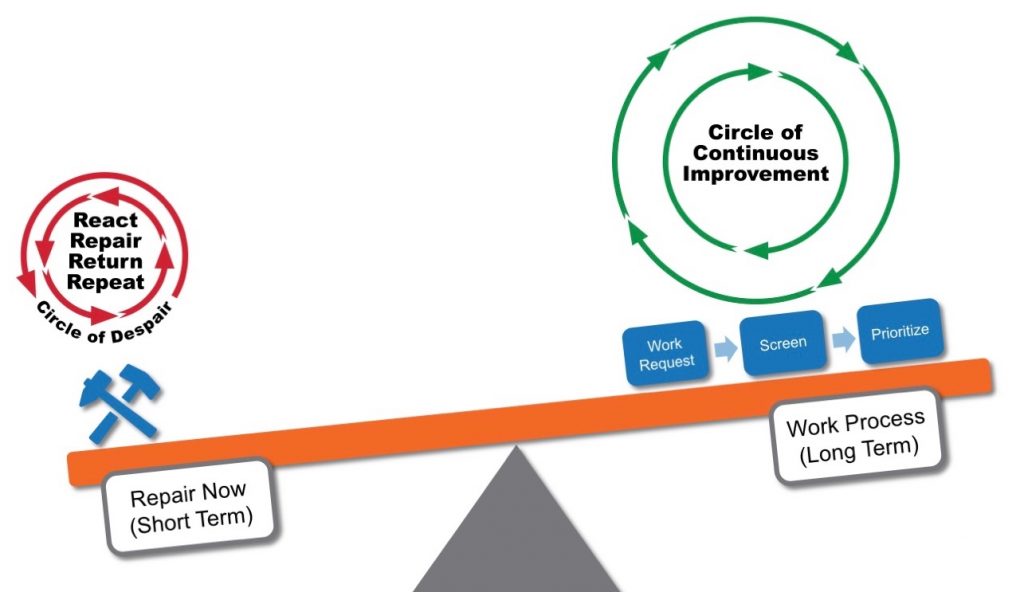
Most problematic maintenance organizations are working on taking care of problems that happened today or yesterday.
Therefore, there is no time for planning and scheduling of jobs. Repairs are done with poor quality since there is often no access to the right tools, materials, instructions, drawings, etc. The poor-quality repairs lead to rework down the road which in turn leads to an even more reactive organization. We call this “the circle of despair” at IDCON.
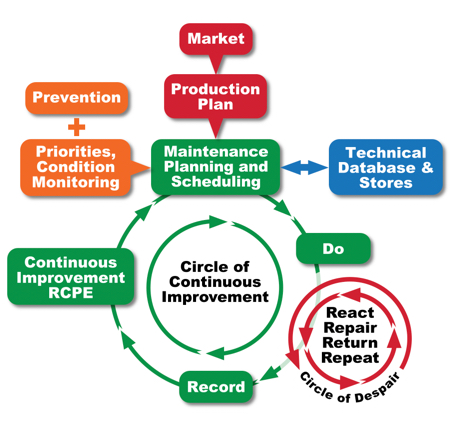
If an organization in this situation is told to target quick results, they often select a few critical pieces of equipment and start to repair known problems. The organization typically adds some overtime and contractors into the organization to work on the known backlog.
This approach will provide quick results! Quick results are great to instill enthusiasm and energy into reliability projects. However, if they aren’t combined with the institutionalization of basic work management practices, they will not provide long-term reliability.
Especially if we select the most critical equipment and do some basic preventive maintenance (PM) problem-solving at the same time. We use this approach quite often ourselves to show that the process works early in projects.
However, if we don’t work on improving the basic work processes, the equipment will return to the state it was in soon enough and the mill will be back to square one.
This is exactly what was happening at the tissue mill.
They improved a little bit but kept sliding back because they didn’t have a solid work processes in place.
What they need parallel to the quick fixes is the systemization of a basic work process that includes.
- Prevention of failures through, for example, lubrication, operating practices, alignment, precision installation, etc.
- Work Management through Inspection – Planning – Scheduling – Execution.
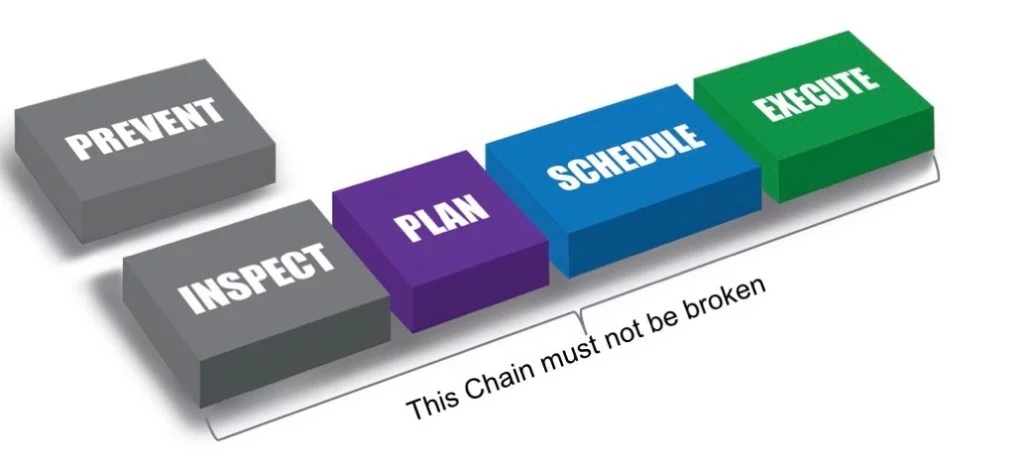
If the mill had worked on some quick fixes at the same time as working on implementing a work process, they would have had a stable OEE, probably in the low 90s range.
Like this content? Watch more of our videos on our YouTube Channel or read more article like this one.