We cover a lot of ground in this article.
Below is the table of contents to help you navigate.
What is maintenance planning and scheduling?
Maintenance planning and scheduling are two key elements of the total “Maintenance Work Management Process”. The planning and scheduling maintenance work is typically broken into three different work processes.
- Weekly maintenance work
- Daily maintenance work
- Shutdown/ turnaround work.
Daily/ weekly and Shutdown maintenance planning and scheduling intersect with each other, but they are somewhat different in nature. We will mainly discuss daily/weekly planning and scheduling in this article.
The Definition of daily and weekly planning and scheduling
Daily/ weekly planning and scheduling deals with all maintenance work in a plant/mine including preventive maintenance work, corrective maintenance work, and improvements that are not capital work.
While maintenance planning and scheduling is central to the process it is part of the whole work management process. In summary, the major components of the work management process consist of:
- Work identification
- Work request
- Prioritization
- Planning
- Scheduling
- Execution
- Recording
- Backlog Management
What is Shutdown planning and scheduling?
Shutdown planning and scheduling is a process for completing maintenance work when a plant/ mine is shut down from production. Since most equipment is down, there is an opportunity to complete a lot of maintenance work.
Shutdowns can be small, a pit stop in car racing is seconds, in most plants it can be from minutes for a manufacturing change set up too few hours, to several weeks long. Maintenance planning and scheduling becomes more complex with the length, size, and number of jobs of the shutdown.
The planning process is almost identical in shutdowns and day-to-day work, but the scheduling and other preparations is managed in a different way.
Read these posts about Shutdown Planning and Scheduling to learn more
What is the difference between maintenance planning and scheduling?
Let’s figure out the difference between planning and scheduling by clearly defining each term. Then we’ll define the key steps that should take place in your organization to have a well-functioning process.
“Maintenance Planning” defines WHAT and HOW
“Maintenance Scheduling” defines WHEN and WHO
It is important to understand that planning is very different in nature than scheduling. They are two very different components in the whole process.
Detailed definition of maintenance planning
A “planned” maintenance job is one that has everything needed to do the job safely and efficiently such as:
- all spare parts
- other materials
- technical information
- tools
- lock out and tag out and other safety requirements
- trades required to do the job
Tasks are described with enough detail to complete the job. Cost and time have been estimated and work can be competed to the required standard within the estimated cost. The finished planned job also includes staging of parts and materials, so they are physically available in staging areas near the job site.
Planning should always be done before scheduling. If a job is scheduled before it is planned, then tradespeople must do the planning and there is no way to know in advance if all things required will be available at the time the job is scheduled. The fact is that a job can never be done without planning and most efficient is that planning is done before scheduling.
Detailed definition of maintenance scheduling
Scheduling is deciding when and by whom the job is done.
A “scheduled” job is one that has been included in a weekly, daily, shutdown or another formal schedule before an agreed upon “cut-off time”. It has a defined start and finish time.
All the resources including tradespeople (by name, not just the role), maintenance equipment, tools and supporting services have been scheduled. The activities for various resources are coordinated to minimize the total cost. Of course, the availability of the equipment is verified and coordinated with operations.
As a rule, it is most efficient to first decide when the job must be done and then assign people to schedule. You should schedule to the work and then people.
What are cut-off times?
The cut-off time will be different for different types of plants and types of maintenance activities a plant has. Typical cut-off times in process industry can be:
- Daily schedules: 11:00 am the day before
- Weekly schedule: Noon Thursday before end of week.
- Small Shutdowns (less than 12 hrs.): 1 week
- Larger Shutdowns (12-24 hrs.): 3 to 4 weeks
- Etc.
This means that a job that is put on the schedule 4 pm today to do tomorrow, is an unscheduled job (We call it a break-in job) for the daily schedule compliance.
A job that is put on the schedule Friday morning for Tuesday next week is an unscheduled job for the weekly schedule compliance, but it can become a scheduled job for the daily compliance.
Plants should strive to focus on weekly compliance, but it may be necessary to measure both weekly and daily compliance if you currently work in a reactive environment.
It is important that you establish clear rules for schedule cut off times because you will use these as important Performance IndicatorsM
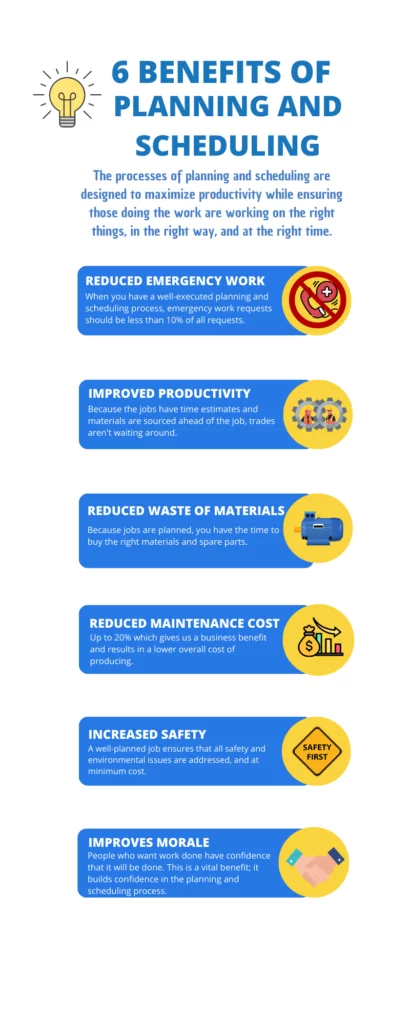
The purpose of maintenance planning and scheduling
The purpose is to complete jobs safely, with best quality (Precision Maintenance) and efficiently at the right time and that work is fully coordinated, between jobs, and between operations and maintenance and others involved, with no delays.
To summarize, the main purpose is to reduce downtime, maximize productivity while ensuring that tradespeople and contractors are always working on the right things, doing them the right way, and at the right time.
Another purpose is to coordinate core maintenance activities and processes with all the stakeholders involved.
What are the benefits of a well-executed process?
Some of the key benefits of a well-executed planning and scheduling process are:
- Less downtime since jobs are completed more efficiently.
- the reduction of emergency work to less than 10%. This will then free up additional resources for you.
- better utilization of Tradespeople due to a substantial improvement in maintenance productivity.
- improved safety and environment results because a well-planned job ensures that all safety and environmental issues are addressed, and at minimum cost.
- Integration of operating and maintenance activities. We never have two schedules, this is critical in shutdowns, and operating jobs can and should be planned also.
- People who want work done have confidence that it will be done. This is a vital benefit; it builds confidence in the planning and scheduling process.
- Reduction of maintenance cost by up to 20% which gives us a business benefit and results in a lower overall cost of producing.
- improved work quality.
- reduces the waste of time and materials, and we avoid buying material that won’t be used.
- highest value work is done first
- increases motivation of all the people involved because a well-planned and scheduled job will allow them time to do a professional job
What are the steps in planning and scheduling?
In the workflow image there are several processes or steps in the overall planning and scheduling process.
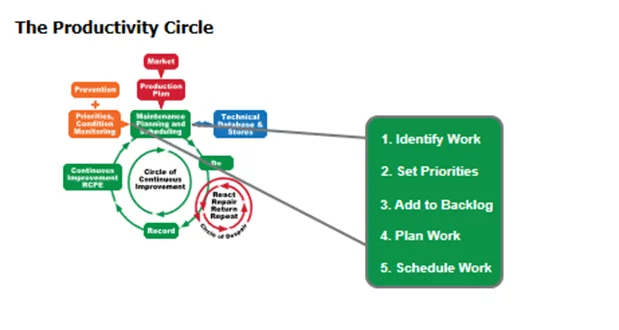
Identify Work
How is maintenance work identified? In most organizations there are three ways that maintenance work is typically found.
- Resulting from basic Preventive Maintenance inspections and Predictive Maintenance and Essential Care.
- Observations by anyone in the plant/mine
- Identifying failures and work needed when doing corrective maintenance work
- When doing non maintenance work activities.
Request Work
When work has been identified, the best practice is to fill out a work request or notification. We recommend using your CMMS system. All employees should have access to the system to request work. Those work requests are then reviewed and approved.
Who reviews and approves requested work?
The person who reviews and approves the request is important. IDCON believes the best is to have one point of contact between operations and maintenance. This function can be part or full time. The function to do the reviews and set requested priority is an Operations-Maintenance Coordinator (OMC) along with a maintenance supervisor.
There should be one OMC function for each maintenance area. Learn more about this vital function by watching this video. These two roles working together will create promote the important partnership between operations and maintenance.
Setting work request priorities
When the OMC or maintenance supervisors review the work request and decide the final priority. They should confirm and adjust the work priority if it doesn’t match the priority guidelines established and agreed upon by operations and maintenance.
It’s human nature for people to think their own job is more important and many times put unrealistically high priority on their work request. This happens a lot in in reactive work environments with a large backlog. And this breeds a lack of confidence that the maintenance team will use a realistic priority.
here are many techniques for setting work priorities, but it should be based on sound logic and importance of safety and other consequences of using higher priority than necessary. Remember to keep priority guideline simple.
There are only two priorities
1. Do the job now as an emergency, and
2. Latest completed date.
If you haven’t defined your work priorities, we have a simple but effective, work order priority guide you can download.
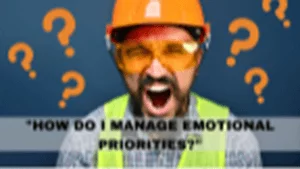
Priorities should be based on the risk if the work is not done within a defined timeframe. For process equipment that time frame could be the next scheduled shutdown if it cannot be done while manufacturing process is running.
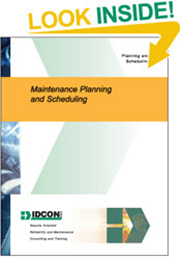
For a deeper understanding of priorities, you should purchase our book Maintenance Planning and Scheduling.
What is maintenance backlog?
Backlog is defined as the volume of work for maintenance that is waiting to be executed. You should have three backlogs.
- Requested backlog.
- Waiting planning backlog
- Planned Backlog. Best practice is to schedule work from the Planned Backlog.
Managing the backlogs is an essential component of good maintenance management. The backlogs should be frequently reviewed to keep it orderly and within targets. Maintenance managers are often tasked to “reduce the backlog size” but be warned, a backlog of zero hours is not a good thing! Backlog is the “Goldilocks” of maintenance – it can’t be too small or too large.
The best practice is to measure the trends of the backlogs, not just the size.
-> Not sure how to calculate your backlog – watch this short video.
Planning maintenance work
The next step in the process is planning. As mentioned early in this article, planning is the “What” and “How” and time estimate of a maintenance job.
The simple fact is that every maintenance job is planned by someone because at some point in any maintenance job, someone must decide exactly what will be done and how to do it.
Unfortunately, we’ve seen all too often it’s the tradesperson who does this because work was scheduled but not planned. This is an ineffective way to perform maintenance work, even in an emergency.
This can cause safety incidents, drives up the costs, may lead to re-work because work is often done under time pressure, and will also take much longer time because the right materials and parts might not be available.
A more effective way is to have dedicated maintenance planner(s). We won’t go into detail about what a maintenance planner does in this post, but for more detail you can read our Maintenance Planner article or watch our Maintenance Planner “What’s my job” series on our YouTube channel.
The planner will go through a series of steps when planning a job. Our planner’s check list is a great resource for any planner to use.
Why it’s important to plan maintenance work
A key to maximizing reliability through improved maintenance performance is to ensure that all work is of high quality. When a job has been planned, the necessary details to complete the job are defined, the right materials and parts are available, and the right resources are identified. Another benefit of true maintenance planning is safety, a planned job is a safe job.
Scheduling maintenance work
Perhaps the most fundamental aspect of managing maintenance is deciding when to do the job and then assigning a job to a tradesperson(s).
Best practice is to schedule work from the planned backlog.
A scheduled maintenance job is defined as one that has been included in a weekly, daily, shutdown or another formal schedule. It has a defined start and end time, and all materials, parts and resources are assigned and the activities for resources are coordinated to minimize total cost.
The purpose of preparing a formal schedule for all work is to ensure that the assignment considers all aspects of the work being scheduled, all other work that may interfere or use the same resources and all operating requirements.
Who should schedule maintenance work?
Every maintenance job is scheduled by someone at some time. We believe the front-line supervisor is the natural role that should prepare the schedule as they know the team best, however, if the maintenance supervisor is too busy responding to reactive work, they will not be able to complete and publish the schedules at the optimal time.
In this instance, we suggest another person be assigned the scheduler role. In some cases, it could be a planner, but this is not ideal.
Best practice is to communicate the next day schedule to tradespeople at end of day’
Worst practice is to post work orders and then tradespeople select what work to do.
What skills does as scheduler need?
A scheduler needs to be able to think logically through variety to complex situations to build a schedule that provides maximum value to the organization. Additionally, they need a good knowledge of the abilities of their trades. Finally, they need to understand the work that is to be scheduled.
If your scheduler doesn’t understand equipment, they will not be able to adequately schedule the right resources. They should involve tradespeople who shall do the work when scheduling the work. This should also be the case when planning work.
Where should they make the schedule?
It takes a lot of concentration to create a daily, weekly and shutdown schedule. There are a lot of moving pieces to consider. It’s imperative the scheduler has the time and quiet environment in which to create the schedules. They also need a printer and wall space to post and review the schedules they create.
What’s operations’ role in the scheduling process?
We discussed how having operations play a role in planning is ideal with a coordinator working closely with maintenance. It’s equally important in the scheduling part of the process.
Some of the support operations must give includes (but not limited to):
- Ensure priorities for all work in the maintenance backlog are kept up to date
- Confirm all shutdown plans in time for them to be fully integrated in the scheduling process
- Manage process inventories (work in Progress) to maximize maintenance access to plant and equipment and to minimize loss
- Plan and schedule all operating activities that impact maintenance
- Attend all priority-setting and scheduling meetings, on time
- Integrate operating and maintenance schedules into a single document, far enough in advance to allow scheduling deadline to be met
For more in depth information about scheduling, we recommend our book Maintenance Planning and Scheduling or to attend our next work management planning and scheduling course.
We’ve assessed hundreds of plants and overwhelmingly the process of work management planning and scheduling of daily and weekly work is an improvement opportunity. The average planning and scheduling score is 35 out of 100, that’s a lot of opportunity for improvement!
What Key Performance Indicators (KPI’s) Can be used for monitoring the planning and scheduling process.
Implementing a better Work Management process
For success you need to get support from leadership. They need to support what needs to be done by being Engaged, Visible and Caring. Develop an implementation plan with implementation milestones for implementation and expected benefits in a business case.
Remember to keep it simple.
- Involve Operations
- Develop the work management process together with operations and arrived at an agreed-upon process, decide on priority guidelines, etc.
- We recommend you start with a simple overview process as an introduction and “selling” your plan.
Below is an example of the overview process and where operations and maintenance roles are suggested
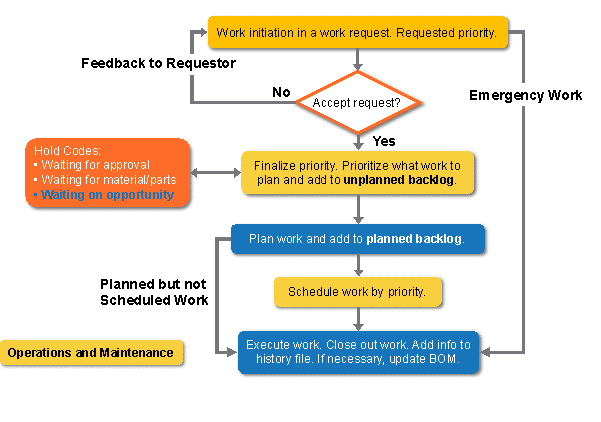
Following this you need to develop a more detailed work management process that includes all involved roles, meeting times etc.
To do this efficiently you need to use a special tool. We use 2c8 software to create detailed workflows that tie roles to each activity.
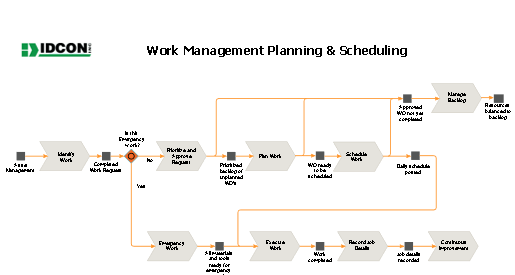
Coaching Work Management implementation
The planning and scheduling process needs to be defined as described above, but the toughest part of implementation is to change people’s behavior and follow the process. We’ve found the key to success is to have a coach to ensure the process is implemented and executed according to the workflows, roles, and responsibilities.
The coach can be an internal resource and/or a consultant. The coach needs to be able to change behavior in the organization by:
- Tell (train) people in the workflows, roles, and responsibilities
- Show the organization in the field how to perform each role (planner, supervisor, OMC, etc.)
- Do together with the organization and work with the core team side-by-side.
IDCON uses this approach when coaching our clients, for example, when we coach planners to become better planner, we follow the three steps above.
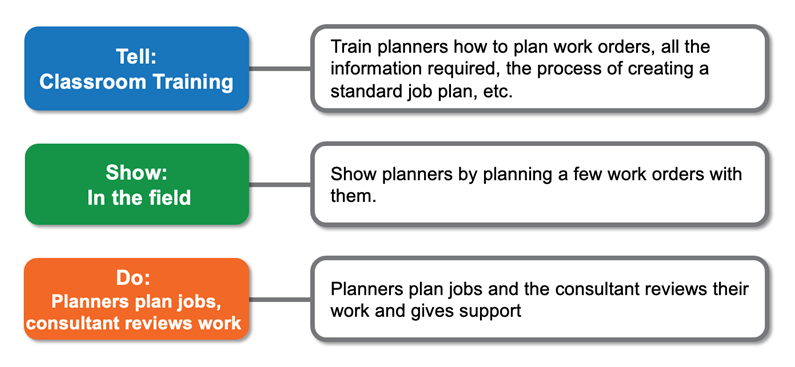
Key Performance Indicators (KPIs) for planning and scheduling
If your organization is very reactive, for example over 30% of all daily work not planned and scheduled the day before it can be a waste of time to measure schedule compliance because you know it is poor.
It would be better is to measure what causes the break in work and then take action to improve these causes.
Some reasons why break in work happens are
- Priorities of work is set too high
- Emotional priorities – I want it done now!
Be realistic, set as a goal for each maintenance area, to bring down break in work to less than 10%.
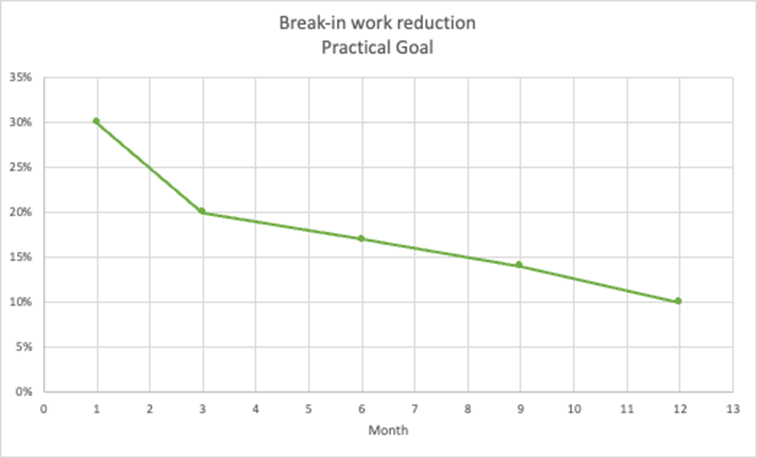
Post the chart and plot results on weekly average.
Once your break in work is under control, you can then start measuring other leading indicators, such as,
- the percentage of schedule compliance
- percentage of planned work in schedules
- percent of preventive maintenance (PM) compliance
- percent of work identified from PM inspections by operators, tradespeople, and Predictive Maintenance
All these leading indicators drive the lagging indicators in the right way, for instance, safety incidents, Overall Production/Manufacturing Reliability, product throughput speed, Maintenance cost, and more.
Wondering how your plant will measure up?
Contact us for a deep dive assessment of your planning and scheduling process.
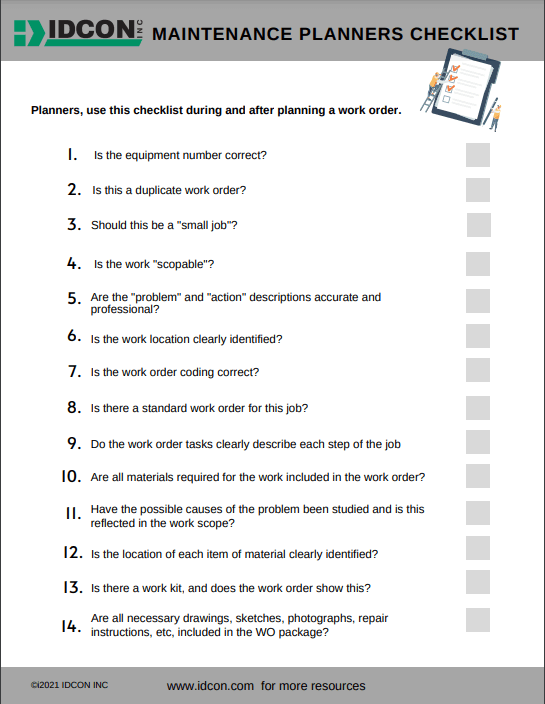
Download IDCON's Maintenance Planners Checklist (part 1)
This 28 point checklist is a great starter document make sure you’re on top of your maintenance planning.
At IDCON, we understand the pressure you face trying to build a reliable plant.
We provide side-by-side reliability and maintenance consulting and training designed to keep your equipment running.
For over 45 years, we’ve partnered with 100s of manufacturing plants around the world to eliminate the costs and the pressure caused by unreliable equipment. And we’d love to do the same for you.
Contact us today to see how we can help you keep your plant running.
Related Articles
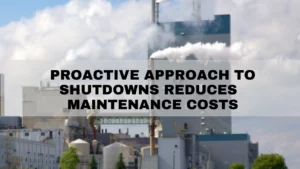
Proactive Approach to Shutdowns Reduces Potlatch Maintenance Costs
Potlatch Cloquet’s low-cost maintenance shutdown management techniques focusing on type, quality, and timing of work contribute to an 83% drop in maintenance cost per ton. Effective shutdown management is critical
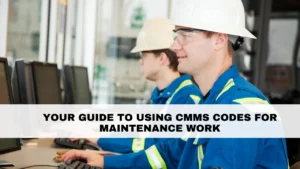
A Helpful Guide for Using CMMS Codes in Maintenance
This article provides guidelines on the selection and structure of the codes and categories that CMMS Software work order systems use to filter and sort backlogs of work. When many
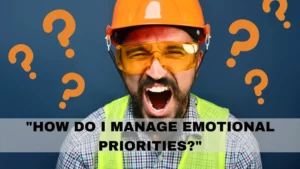
Setting Disciplined Priorities when Prioritizing Maintenance Work
Setting Disciplined Priorities – A Maintenance Planning and Scheduling Perspective Priority, as defined in the Franklin Dictionary, means “coming before in time, order, or importance.” When prioritizing maintenance work, one
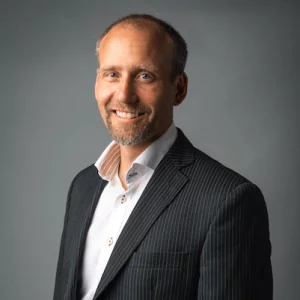