To put it simply, the main responsibility of a Maintenance Supervisor is to ensure that maintenance work is executed. But what are the essential skill set required of this position? What is their role in work execution, reliability and maintenance and maintenance planning and scheduling?
To perform this job well, a good Maintenance Supervisor must have competent technical skills so they can understand the work their crew is doing. Often, former Craftspeople and Reliability Engineers turn out to be great Maintenance Supervisors because of their hands-on experience.
What skills do they need?
To perform this job well, a good Maintenance Supervisor must have competent technical skills so they can understand the work their crew is doing. Often, former Craftspeople and Reliability Engineers turn out to be great Maintenance Supervisors because of their hands-on experience.
Being a strong leader while working as a team and communicating effectively is an essential part of being a Maintenance Supervisor.
One of IDCON’s core beliefs is that people cannot be more productive than the system they work in allows them to be, and this definitely applies to Maintenance Supervisors. We have seen all sorts of situations, from the Supervisor running the crew in the field, to Supervisors acting more like managers. This can make it unclear what the Maintenance Supervisor should be doing – which can result in people ending up doing what they think they should be doing rather than what they should be doing (it’s just human nature).
A well-functioning system
Let’s imagine a well-functioning system. There is a Maintenance Planner dedicated only to planning, a Reliability Engineer focusing on documenting PMs and Root Cause, and an Operations-Maintenance Coordinator (OMC) working with Production to screen work orders and prioritize daily work.
So here we have the Planner focusing on the next month or months ahead and the OMC focused on daily priorities. Who is thinking about the weeks ahead? Who is scheduling the crew for the planned work? This is where the Maintenance Supervisor comes in.
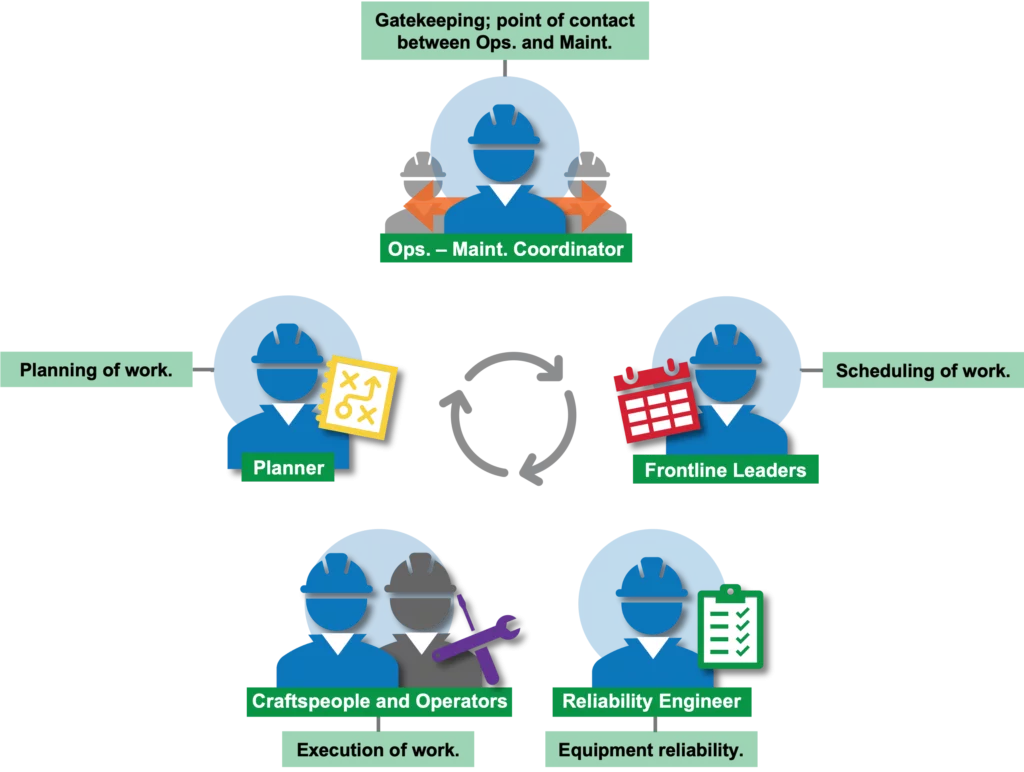
While we see a lot of Planners taking on the scheduling function, we think that the Supervisors should handle the scheduling of weekly work. They know the crew better than anyone, so they know who is working when and whose skills are best used where. This allows the Planner to plan important tasks such as ordering parts, determining the need for contractors, and organizing long lead times.
As mentioned before, they must be technically skilled and understand the job steps. So, it makes sense for one of their key roles in execution to be scheduling the crew to reach that main goal. This position functioning correctly can help your organization achieve world class maintenance.
In our next video, you’ll learn about other key responsibilities of the maintenance supervisors.