An effective Preventive Maintenance program should result in better equipment and production quality.
Let’s look at the tasks you need to develop and manage your preventive maintenance program through the eyes of a new Reliability Engineer. This RE works in a plant that currently lacks documented procedures. Want to learn more about what a Reliability Engineer’s job role is? Watch our YouTube “What’s My Job Series” of videos.
You have been asked to document your own Preventive Maintenance Program (PM’s) for the plant and a target of 6 months to complete the project.
- The plant has around 5,000 pieces of equipment.
- A corporate initiative to increase output and reliability of product deliveries is the reason for developing and documenting the PM procedures.
- The plant runs from 5/24 to 7/24 depending on the market demand.
Besides the issue with how to manage this as a project and using a CMMS to manage and maintain the procedures and history, I want to help you focus on how to select and document your preventative maintenance procedures in a practical way. Note that most PM procedures should focus on equipment at the component level like bearings, packing, impeller etc.
In some instances you may want to use RCM or FMEA for your most critical equipment, but in our view it’s much quicker to use IDCON’s Condition Monitoring Standards to document, especially if your preventive maintenance program is not functional. The advantage of the CMS documents is that they not only tell the “what” but also the “how” to inspect and care for equipment. You can download two of our standards for FREE.
How do you decide when to use each documentation method for asset/equipment? Selection Criteria for RCM or FMEA can be guided using these criteria:
- Complex operation not fully understood
- Poor reliability performance (consider doing an RCA first)
- Highly automated (complexity)
- Multiple integrated functions (complexity)
- New type of equipment where experience levels are low (nonstandard assets)
- Regulatory requirements
Again, using CMS method can be used for 95% of equipment. So, how do you start documenting your PMs? First, we suggest starting with a pilot area so that you aren’t overwhelmed. Then use our 5 step documentation process.
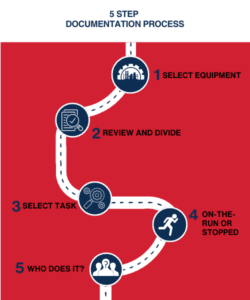
5 Step Documentation Process
Step 1: Select your equipment. You’ll need to gather your equipment list/GA/P & ID, equipment number/name, and finally describe its operating context.
Tools used: equipment list, general arrangement drawings, process, and instrumentation diagrams (P&ID), and operations procedures (SOP). How can we find out what the operating context is? The answer may be obvious, or we can ask the operator, review the operating SOP, or use the process diagram to figure it out. What happens if the function is no longer working? Does it cause a risk of environmental impact or personal injury, high cost due to lost production or damaged product, and preservation value of the equipment life?
In this step, you’ll also perform a criticality assessment.
Step 2: Review the equipment in the field and divide the equipment into its various components.
Review the documentation for the equipment but confirm that the equipment and components are the same in the field. This is necessary because changes in the plant may not match the documentation, or it may not have been updated as built. Take notes on what components you see and any other observations that impact the inspection. Collecting pictures is a good way to document as you may need to review the information again. Pictures of the equipment may also be used to save in the technical database to visually identify the equipment.
Some other questions to ask:
- How does the component work?
- How does it fail?
- What essential care does it need?
- Is the life of the component predictable or unpredictable?
- Does it have a Failure Developing Period (FDP)?
Step 3: Select Task. You need to determine what essential care and condition monitoring tasks need to be done for each component in the equipment.
After reviewing the equipment in the field, confirm that the documentation is up to date. Another task we recommend is to assess the condition at the same time as developing the PMs. IDCON’s CMS books have the instructions for how to care for and inspect equipment using keywords that can be referenced in your PM inspection or route, you can also use the OEM’s instructions as another source, however a note of caution, sometimes the OEM’s frequencies may not be correct for your operating context.
Step 4: What condition (on-the-run or stopped) can the Condition monitoring or essential care task be done?
On-the-Run inspections are much more economical since shutdown time means lost production. Running inspections also will tell you more about the equipment condition, such as pressures, temperatures, vibration, noise, and visual. But of course, there are some tasks that must be done stopped.
In this step, you’ll also determine the tools you need to use for the tasks and the frequency of the inspections and care tasks.
Step 5: Determine who does the task
Use a decision tree to determine who should do the tasks. The groups that should be considered are: Operators, Area Maintenance, In house specialists (Vibration Analysts, etc.), and Outside specialists. Download our Autonomous Maintenance (operator based maintenance) implementation guide.
Developing a successful Preventive Maintenance program is critical to your plant’s success.
But knowing whether you’re doing the right things at the right time can be hard. IDCON can help your team with developing and documenting your Preventive Maintenance program, including using our technical consultants to document the PMs for you! We start by assessing your current program’s documentation and execution and help you develop a plan.
For a deeper look at developing your own Preventive Maintenance Program, download our free 8-Step Guide (and supplemental training video) below.
Trying to develop your own Preventive Maintenance Program?
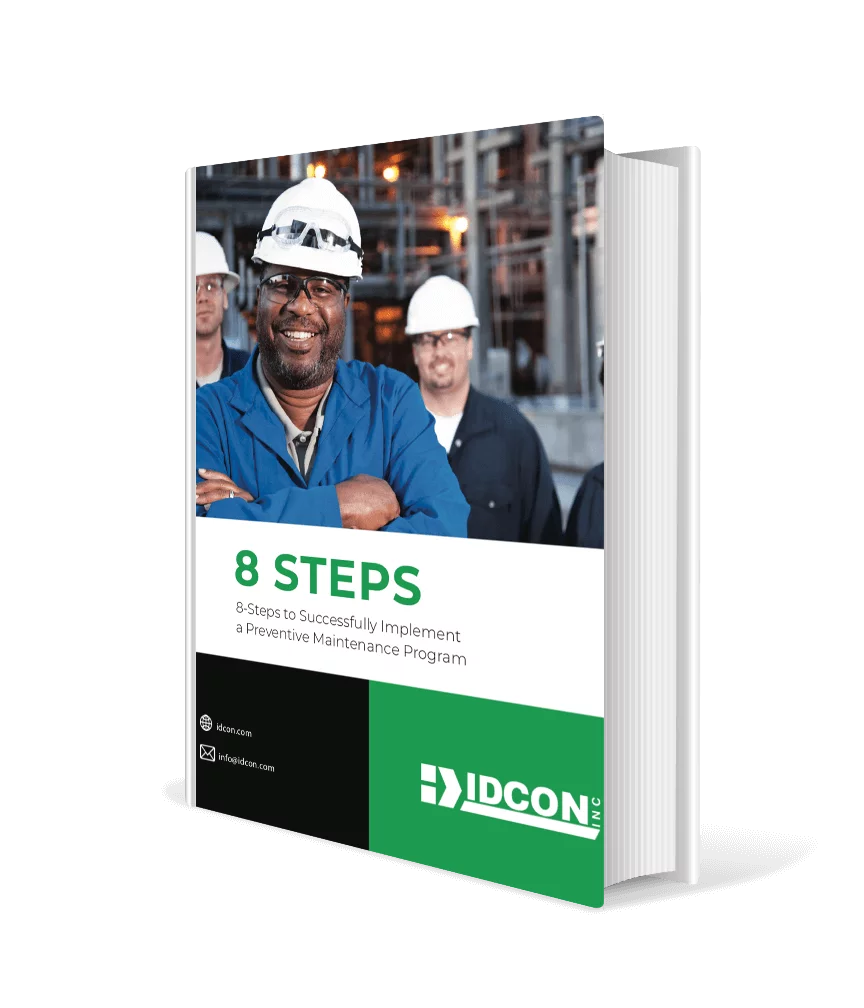
Download our free 8-step guide to successfully develop your own Preventive Maintenance Program DOWNLOAD HERE