Root Cause Failure Analysis – IDCON’s Root Cause Problem Elimination Process
We have named our process for problem solving training and elimination “Root Cause Problem Elimination™” instead of the commonly used Root Cause Failure Analysis (RCFA).
We believe Root Cause Problem Elimination™ better describes the desired results of a Root Cause process. Root Cause Analysis (RCA) indicates that the desired outcome is to analyze the root cause of a failure. The desired outcome should be to eliminate the problem.
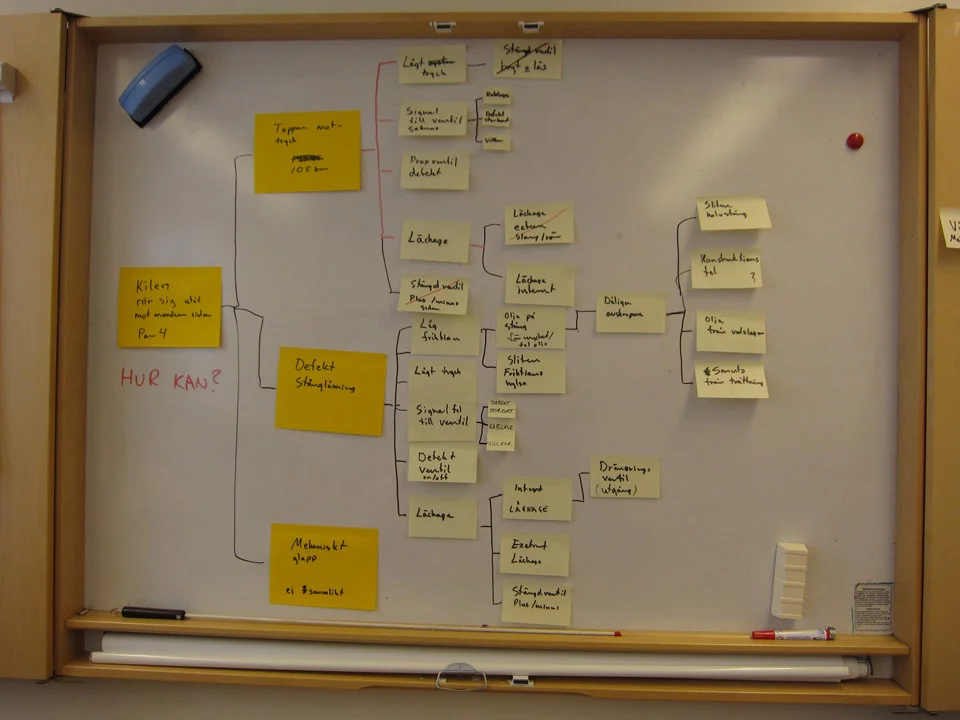
The basic concept of any problem solving method is to use a number of structured steps to arrive accurately at the true source of the problem in order to eliminate it.
IDCON’s consulting and training focuses on what we believe most plants need:
- A simplified, structured, practical approach to eliminating problems for the frontline (hourly & first line supervision), to enable root cause analysis and elimination of problem on the plant floor.
- Training and support for facilitators when going through root cause analysis and problem solving sessions
- Support to implement a complete root cause problem elimination business process for the plant
We see that 80-90% of all problems can be eliminated by training and implementing basic problem solving methods for the frontline organization (operators, craftspeople, planners and first line supervision).
The remaining 10-20% of the problems that are harder to solve should go through more structured problem solving where more people are involved.
The second level of problem solving requires facilitator support.
Training is important, but the RCPE process must be embedded in your organization to be sustainable. This process includes:
• How to record problems.
• How to select problems to be analyzed.
• What triggers are to be used.
• How to document solutions.
• How to share results within your plant and between several plants.
• Use results for autonomous training.
The training classes we offer are:
• Root Cause Analysis Training for the frontline organization
The implementation support and on-the-job training includes:
• Design and implementation of the work processes, documentation, and measurement of RCPE.
• On-the-job root cause analysis using your problems
• On-the-job training for facilitators of Root Cause Analysis