Setting Disciplined Priorities – A Maintenance Planning and Scheduling Perspective
Priority, as defined in the Franklin Dictionary, means “coming before in time, order, or importance.” When prioritizing maintenance work, one must consider its importance to the entire company in question. My experience shows that, in the real world of most maintenance departments, you can classify priorities in two groups: Emotional priorities and real priorities.
EMOTIONAL PRIORITIES.
An emotional priority is one that is based on feelings instead of objective judgment of importance. The importance of the maintenance work is judged only as it relates to the production area where the requester works.
For example, a person in operations might want to have a maintenance job done just to get it off of his or her mind. It is common to see that many of these types of priorities are requested using a standing work order number or are requested verbally, bypassing the use of a computerized or manual maintenance work request routine.
Because maintenance acts as service to operations, these methods of requesting maintenance work will continue to increase if written work requests and strict disciplines for standing work orders are not enforced. This happens because it is more convenient for the requester to have someone else document the work request than to do it himself.
Another reason why emotional priorities are common is that they often provide the only way to get a maintenance job done within a reasonable time frame. Requesters of work know when everybody in the organization is abusing the priority system.
They also know that if they try to be nice and instate a lower priority than is necessary, their specified job will never get done. Ultimately, this means that the work request will be pushed through with a higher priority than necessary.
Jobs with emotional priorities, as well as true emergencies, will bypass the planning and scheduling process and consequently cost more money.
REAL PRIORITIES.
What I call “real priorities” are based on the importance of the work to be done and its benefit for the whole company or production area.
The priority of the work is based on the consequence of not doing the job and the condition of the component as measured during a component inspection. In a good organization, up to 90% of all maintenance work is a result of condition monitoring, including basic inspection routes and interviews with operators. With real priorities, more work can be planned, and after that it can be scheduled and executed in an efficient way.
A SOURCE OF CONFLICT.
Requesters of maintenance work often have only their own production area in mind when prioritizing maintenance work, while their maintenance partners are often faced with ten “priority one” jobs from different requesters when they can only accommodate five.
This results in conflict with the people who don’t get their jobs performed. And to make matters worse, it is often the people who give the maintenance planner or supervisor the most problems if their jobs are not done who get precedent.
This is often done at the cost of others who might have had a more real need for a completed job.
Setting Disciplined Priorities – Confront the Problem!
I know that many readers recognize the type of conflict I have described as if it had been taken from their own mills.
How to prioritize maintenance work orders:
I like to offer the following actions for changing the state of the maintenance process from being reactive to being planned, scheduled, and controlled:
- Set up a task force between operations and maintenance with the objective of arriving at more disciplined priorities.
- Educate key people about the importance of using the right priorities. Teach them that it costs several times more to do a job that breaks into a set schedule than to do a job that is planned and scheduled.
- Agree that operations and maintenance will decide priorities together according to well-defined guidelines. The only jobs that justify a “priority one” (immediate action that breaks into other ongoing jobs) are jobs such as the following:
Immediate risk for personal injury or environmental damage.
Production line is down, and, for example,
there are no buffers of paper to keep a coater running until the job is performed.
Immediate risk for production loss or high maintenance costs.
All other jobs, which should be included with examples in the priority guidelines, should be prioritized with a requested date for latest completion. For example, if a pump that has back up fails, it will not automatically constitute a “priority one” job.
Determining and using new priority guidelines will yield faster results with fewer breaks in work and increase the planning, scheduling, and control of maintenance. However, count on the fact that even this simple process of implementing guidelines might take time
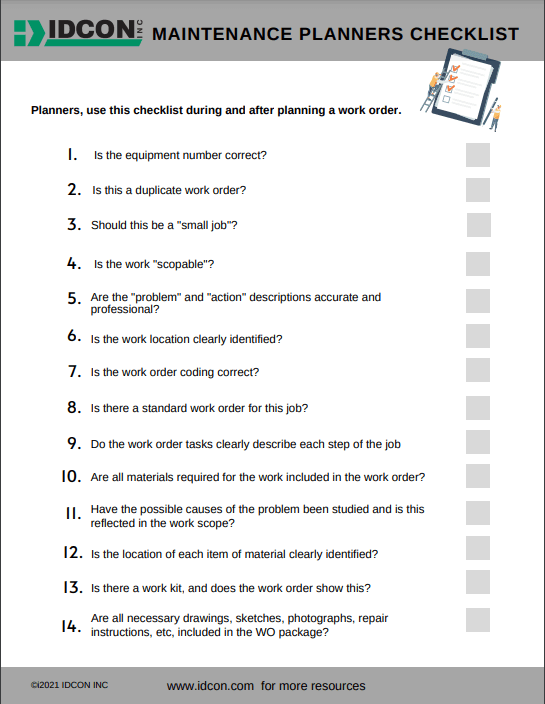
Download IDCON's Maintenance Planner Checklist (part 1)
This 28 point checklist will get you started on planning your own maintenance work.