Are you finding it difficult to manage your maintenance and reliability resources? Do you feel like you cannot catch up on the work order backlog?
Backlog Management is the main objective in managing maintenance in a plant or facility. The key results of backlog management are completing work in a timely manner and managing the long-term demand for resources.
What’s timely?
Timely is defined as being proactive to avoid production losses, increased manufacturing cost, and possibly lose market share. In my experience, many plants struggle to measure the backlog of maintenance work. This is often because it can be difficult to calculate the backlog and use that to measure if maintenance has enough resources to get work done and to meet business requirements.
How do you calculate crew weeks (or weeks of backlog)?
Example: You have 10 techs and they have a regular work week of 40 hours.
10 techs x 40 hours/week = 400 hours/week = 1 crew week
The best practice for the process industry is to have a backlog of 4-6 crew weeks in total for weekly and daily work. If it’s 6 weeks and if no additional work orders are added it will take 6 weeks for the crew to finish all work orders during regular work hours.
Some industries like pharma and food may have best practice targets of about 2-4 weeks.
TIP: Your weekly and daily backlog should be calculated separately from the shutdown.
For shutdowns, the issue becomes more about: ‘Can we operate reliably until the next shutdown?’
I visited a plant experiencing an increasing trend of equipment breakdowns. After reviewing the data, we discovered that the monthly budget target was limiting the maintenance team by cutting out some work that was necessary for the monthly shutdown. We calculated the downtime and available resources and found it would take more than a year before some of the work would be completed at the monthly shutdown. This did not support the reliability goals of the plant.
Balancing the Backlog
Picture the backlog as a series of tanks that have an inlet and outlet. If you add the same number of gallons as you remove, then you have balanced the level or volume in the tank. The same principle applies.
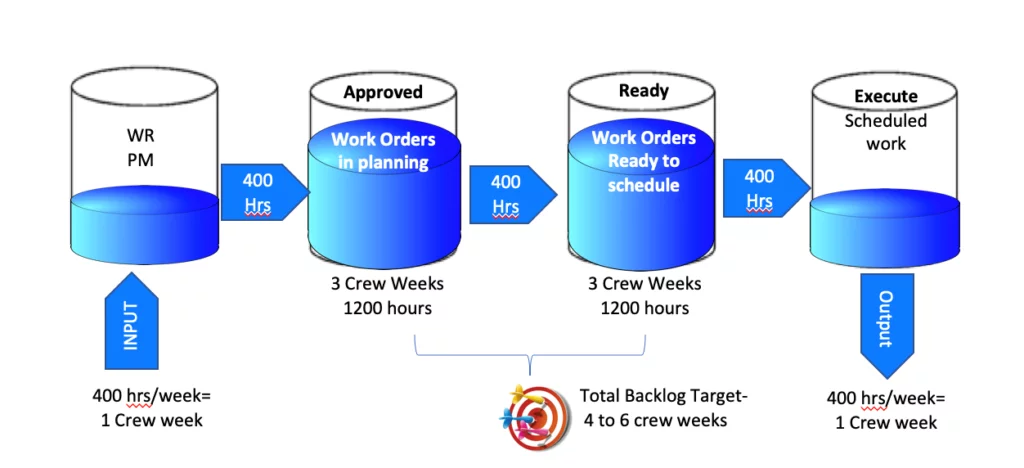
- Example: You have 1200 hours of work orders approved to be planned or in planning, based on one crew week being 400 hours, that equals 3 crew weeks.
- You add another 1200 hours of work orders that have been planned and are ready to schedule, that equals another 3 crew weeks.
The total backlog is 6 weeks (or 6 crew weeks). There should be no backlog of work requests. In the example above there are 400 hours or work orders and PMs added. At the same time 400 hours of work is completed every week, therefore the backlog is in balance and within the target of 4-6 weeks.
Managing this work management process is one of the most fundamental principles of managing the maintenance function. How many hours are in your backlog?
Estimating Time
One of the difficult parts of managing the screening process is approving, prioritizing, and adding a time estimate to the work request. A work request becomes a valid work order only after it has been properly screened.
A client in the chemical industry asked me, “Why do we need to estimate the time of the work order during screening? Isn’t that done in the Planning step?”
To answer the question, I gave an example that happened at another plant “The plant had more than 25,000 hours waiting to be planned or in planning. The client did not know the size of the backlog, they only saw 920 work orders in the system and did not think much of it. Many important corrective work orders had been delayed and caused increased downtime in production.
Example: If your predictive maintenance tech writes a work order to replace the main drive bearing on the motor, based on the failure developing period (or PF-Curve), you cannot wait 12 months to replace it – it will likely fail before that work order is scheduled.
Another factor at the plant that contributed to the issue was that many of the work orders had a high priority code so they could not determine which was most important to do first.
There are no drawbacks to managing the backlog of work though KPIs and measurements can always be manipulated.
The biggest benefits:
- Ensures the maintenance department has enough resources in the long run
- Keeps track of work order aging
- Balances resources between areas, units, and crafts
- Makes sure that no work order is missed.
Why is there resistance to calculating?
- The initial estimate may be wrong, but you are better off having an estimate of the backlog than just a number of work orders.
- Sandbagging times on the work order – may overstate the backlog.
Statement by the Ops Superintendent “The backlog is prioritized so we know what is important and we will do that first, no need to measure the size of it!”
– if the backlog is large then it will take a long time to catch up and during this time most work orders become high priority due to the age. This is what we at IDCON call “the circle of despair”. There is no time to do proactive work like prevention and condition monitoring, so the failures and equipment breakdowns keep growing and many work orders become high priorities and emergencies.
“I’ve calculated my backlog and it’s too big, What can I do to fix it?”
You have four choices to decrease your backlog size
- You can move resources between areas or units
- You can start working overtime
- You can hire contractors
- If there is a long-term trend of backlog increase over at least 6 months, you can hire more craftspeople.
If the backlog is too big, then work will be delayed, and reliability will suffer. Another indication that the backlog is too big is when the organization and, specifically operations, by-pass the work order system because few work orders are getting done in a timely manner.
“I’ve calculated my backlog and it’s too small. What’s the fix?
If it is too small, it is very likely that the team is over staffed – I have not seen that too many times.
If you need help to improve your backlog management, give us a call at 919-847-8764 or email us [email protected]. Or join us for training in Work Management Planning and Scheduling.
Owe Forsberg is Vice President of IDCON INC. Owe has over 25 years industry experience in Reliability and Maintenance management. In his previous position as Maintenance Manager at Novosymes he received the North American Maintenance Excellence (NAME) Award.
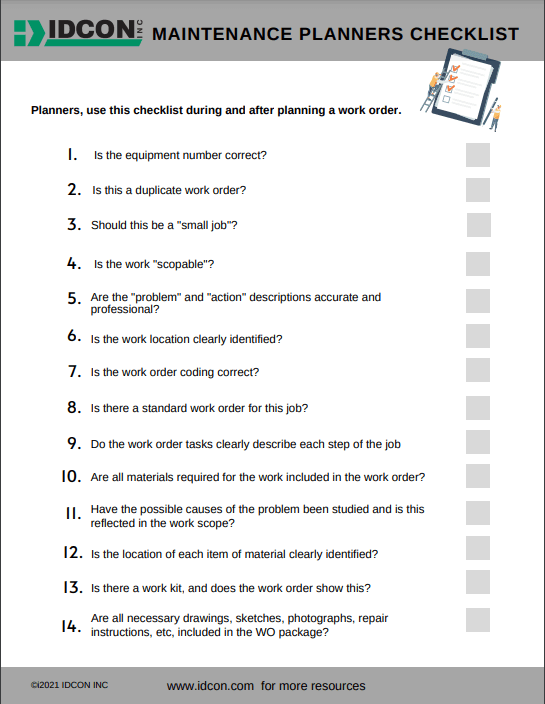
Download IDCON's Maintenance Planners Checklist (part 1)
This 28 point checklist is a great starter document to make sure you’re on top of your maintenance planning.